Understanding Grease Compatibility: A Guide to Smooth Operations
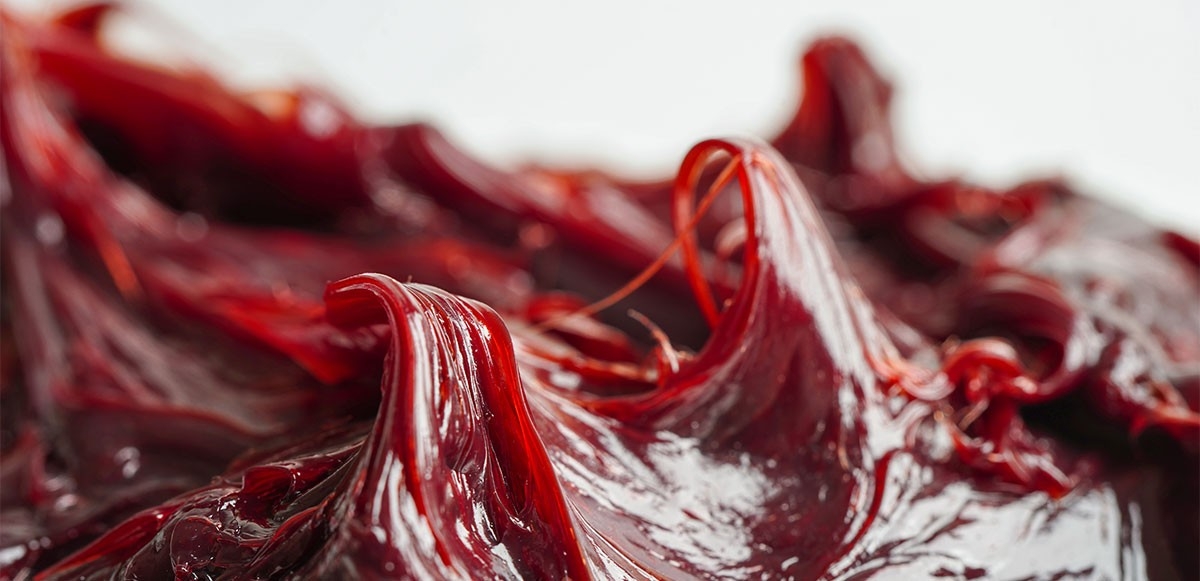
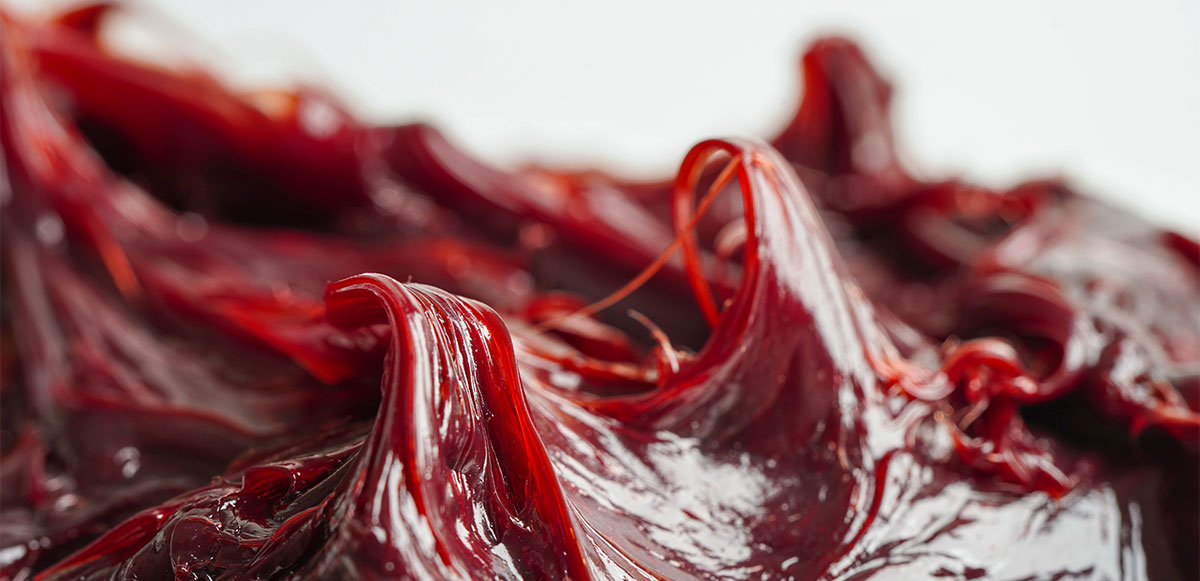
Grease compatibility is a critical factor in maintaining the performance and reliability of mechanical systems. Improperly mixing grease can lead to equipment failure, increased maintenance costs, and reduced operational efficiency. This blog delves into the fundamentals of grease compatibility, its importance, challenges, and best practices for ensuring optimal performance.
The Basis for Grease Compatibility
Grease is a combination of base oil, thickener, and additives. Compatibility between greases depends on the interactions between these components:
Base Oil Compatibility
Base oils, either mineral or synthetic, form the primary lubricating medium in grease. Mixing greases with incompatible base oils can cause phase separation, reduced lubricity, and degradation of the grease’s properties. For example, mixing mineral oil-based grease with synthetic oil-based grease may lead to viscosity changes or chemical instability.
Thickener CompatibilityThickeners provide the semi-solid structure of grease. Common types include lithium, calcium, polyurea, and aluminum complex. Mixing incompatible thickeners may cause grease to soften, harden, or even lose its structural integrity. For instance, lithium and polyurea thickeners are generally incompatible.
Additive CompatibilityAdditives enhance grease performance by providing properties like corrosion resistance, extreme pressure tolerance, or anti-wear characteristics. Incompatible additives can neutralize each other’s effects or create harmful reactions that degrade the grease’s performance.
Categories of CompatibilitySeveral methods are used to evaluate grease compatibility:
Dropping Point TestThis test measures the temperature at which grease transitions from a semi-solid to a liquid state. Mixing incompatible greases can alter the dropping point, leading to performance issues in high-temperature applications.
Worked Penetration Test This test assesses the consistency of grease after it has been mechanically worked, simulating actual use conditions. Significant changes in consistency may indicate incompatibility, which can result in improper lubrication.
Four-Ball Wear TestThis test evaluates the anti-wear properties of grease under load conditions. It provides insight into how well mixed greases can protect surfaces from wear. Incompatibility often leads to increased wear rates.
Oil Separation TestThis test measures the tendency of oil to separate from the thickener in mixed greases. Excessive separation can compromise lubrication and lead to equipment failure.
By conducting these tests, you can identify potential issues before mixed greases are applied in critical systems.
Challenges of Grease Compatibility
Lack of Standardization Grease formulations vary widely among manufacturers, making compatibility difficult to predict. Even greases labeled as similar can behave differently when mixed.
Field Conditions Operational environments, such as extreme temperatures, high pressures, and contamination, can exacerbate compatibility issues, leading to unpredictable performance.
Limited InformationOEMs and suppliers may not always provide detailed compatibility data, leaving end-users to rely on testing or experience to determine compatibility.
How to Minimize Mixing Effects
Standardize GreasesWherever possible, use the same type of grease across similar equipment to eliminate compatibility concerns. This also simplifies inventory management.
Consult OEM RecommendationsFollow the manufacturer’s guidance on recommended greases for specific equipment. OEMs typically specify greases that are tested and approved for their systems.
Flush and CleanWhen switching grease, thoroughly clean and flush the equipment to remove residual grease. This minimizes the risk of mixing incompatible greases.
Conduct Compatibility TestsBefore introducing a new grease, perform compatibility tests under controlled conditions to ensure it will perform reliably when mixed with existing greases.
Maintain RecordsKeep detailed records of the grease used in each piece of equipment. This information is invaluable for troubleshooting and avoiding accidental mixing.
ConclusionUnderstanding grease compatibility is essential for maintaining equipment reliability and performance. By considering the compatibility of base oils, thickeners, and additives, you can prevent costly failures and extend the life of your machinery. Regular testing, adherence to OEM recommendations, and proactive maintenance practices are key to minimizing the risks associated with grease mixing. Remember, a little attention to grease compatibility goes a long way in ensuring smooth operations and cost efficiency.