Varnish Removal Solutions: How Effective Are They?
Hint: A more effective varnish solution is available now!

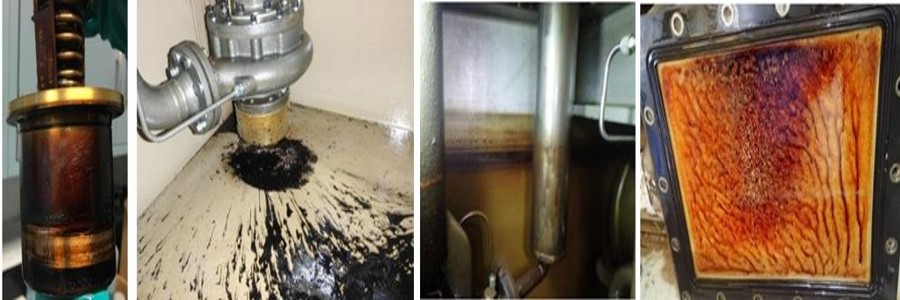
In an earlier article, we delved into the causes of varnish in industrial oil systems. We looked at how oil degradation produces submicron particles that eventually cluster and stick to metal surfaces, turning into varnish. Left unchecked, varnish can lead to varying levels of equipment failure, costly downtime, expensive repairs or, in the worst cases, complete replacement.
Those costs can be mitigated through varnish removal. There are a number of techniques and mechanisms that have proven effective in removing varnish from surfaces. One way is to apply heat to essentially reverse the varnish process. Varnish tends to soften under very high temperatures and will to some extent dissolve back into the oil. Until the oil is changed, the particulate matter will remain in the oil and the problem may recur.
Another way is through chemistry that changes the oil’s “appetite” for holding varnish. Commercial chemical products for varnish removal fall into three varieties or families:
- Solvents: these are typically volatile organic compounds, with characteristics similar to gasoline. Solvents have been used effectively to clean varnish, but they raise a couple of challenges. First, they don’t stay in the oil long. They tend to degrade quickly by design, and they evaporate out of the oil in a short period of time. Solvents can also be very hard on rubber components, such as seals or O-rings in the system. And solvents can also lower the flashpoint of the oil by as much as 90 °C, raising the risk of combustion at a lower temperature.
- Dispersants, detergents or combination technology: Some dispersant/detergent brands are widely used and generally proven effective at varnish removal. However, they may change certain fundamental characteristics of the oil. An important one is water separability. Oil and water will usually separate naturally in a system, enabling operators to remove the water. A chemical detergent, much like a household soap, can make oil and water bond together and emulsify, making it virtually impossible to get the water out. Another downside of dispersant/detergent formulas is that the chemistry tends to attack antioxidants and reduce their life, making them incompatible with the oil for extended periods of time.
- Synthetic solvency enhancers: These have been used effectively, but they are not very aggressive at cleaning varnish off surfaces. They work better as a varnish preventative by keeping varnish precursors in solution in the oil and slowing the formation process. Their effectiveness remains a big question, as does their compatibility with oil.
In addition to chemicals added to varnishing oil, filtration systems have also been used with limited success. Several filtration technologies including depth media, electrostatic, balanced charge agglomeration and adsorptive resin can be employed to remove varnish precursors from the oil before it sticks to surfaces. While all of these have proven effective to different extents in removing varnish precursors from the oil, they can also remove beneficial additives from the oil including foam inhibitors, rust inhibitors and extreme pressure performance enhancers.
So we see that, although these existing types of varnish removal products are commonly used and effective to varying degrees, they also raise some big challenges and issues. Chief among these are water separability, oxidation stability, and seal compatibility. At Caltex, we have been working on a viable varnish removal alternative to address these issues. We have undertaken extensive and rigorous, real-world testing in high-risk environments, where failure would be extremely costly, to ensure we had a product that our customers could rely on with confidence. We will share the results of our efforts with you in our next article on the topic of varnish.
Read more about VARTECH™ Industrial System Cleaner varnish remover.