Proper greasing maximizes equipment lifetime

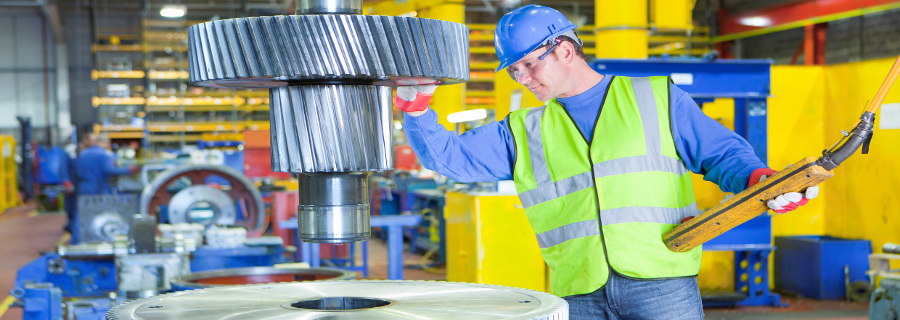
How often re-greasing a particular application is required - is one of the frequent questions customers tend to ask. That however depends on several variables such as the speed of the bearing, contamination level if the unit has moisture, how much of the grease is being used and how high the temperature of the housing is.
Understanding the importance of having the right amount of grease for each application in addition to the re-greasing technique is an essential part of industrial maintenance in both off-highway mobile equipment such as bulldozers, backhoes or excavators and stationary plant equipment.
The standard practice for re-greasing is done by pumping fresh grease which forces out the old grease until the fresh one comes out of the bushing. This procedure gets rid of any contamination from the journal bearing while ensuring that all the old grease comes out. It is a straightforward procedure that requires no measurement or calculation.
Rolling element is a different matter. They often include a shield or a seal to minimize the contamination from spreading to the bearing, ultimately allowing the grease to stay for longer intervals. This however limits how much grease can be applied with each re-greasing. Here, the method of pumping in new grease and flowing out the old grease until the new grease appears, does not work, and is more likely to damage the seals. This inevitably leads to increased contamination, more re-greasing and eventually changing the bearing more regularly.
As a good maintenance practice, taking precautionary measures when it comes to the amount of grease going into the bearing is highly needed. The general rule of thumb is to multiply the bearing width by the bearing diameter in inches, and take one-tenth of that sum which should eventually equal the number of fluid ounces for re-greasing the bearing.
Determining how much grease to put into each specific bearing then adjusting every grease gun in use to find out how much grease is dispensed in one pump can be done using a postal scale. It is advised to cover the scale to keep it clean, and then pump the grease five times onto the scale. Divide the total weight by five to get an average weight of one pump and note this on the grease gun. This number can be used to accurately re-grease bearings.
Over-greasing is one of the biggest problems particularly when it comes to electric motor bearings. It damages the seals or shields and can cause early bearing failure, or even destroy the electric motor.
While there are a few grease choices to choose from, it pays to understand the differences among grease types and how to apply them properly in order to get the optimal performance and longer life from your equipment.
Contact us to know more about the grease that is best suited for your industry and application.