Fueling Efficiency: The Role of Caltex Products in Power Generation applications
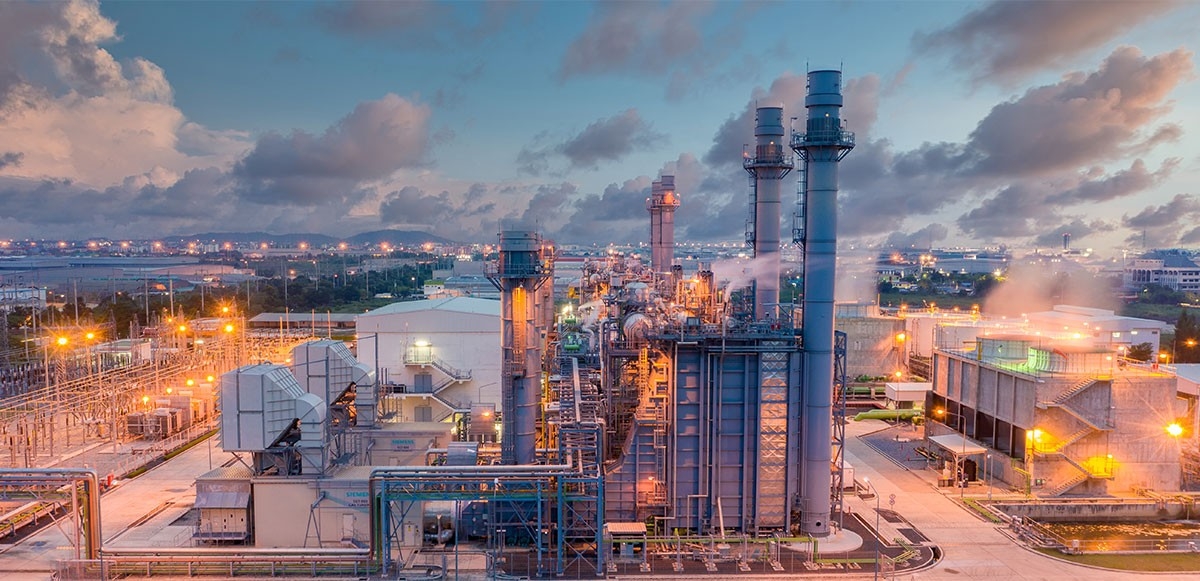
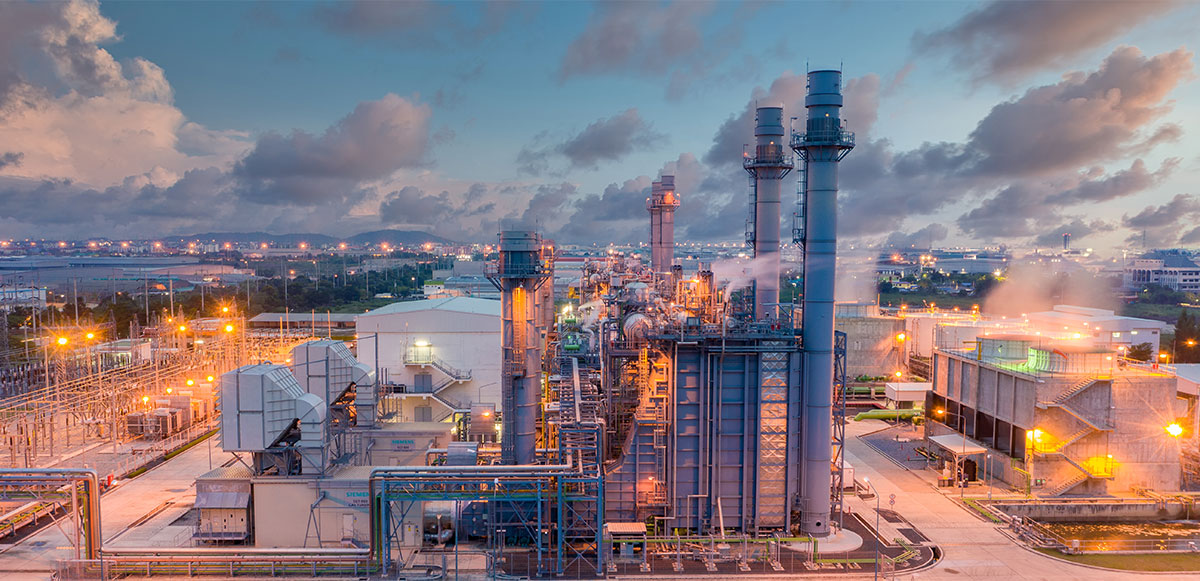
Power plant operations come with a lot of demand. Some of these include heavy and shock loads, high pressure, exposure to hot and cold temperatures, slug, varnish, dirt, and water. All of these and more can adversely impact machinery. Also, since the energy sector can never cease to work, power plant equipment is expected to have zero downtime. That is why it is important to protect the equipment and ensure it operates at full capacity. And a foolproof way of doing so is setting a carefully devised industrial lubrication strategy in place.
In power generation, one can improve energy production and prolong the life of the machines by using the right lubricant, oil or grease.
Industrial lubricants, when used properly, can provide the perfect protective cover for your machinery needs. Power plant lubricants are formulated to target all the shortcomings on the metal surface. They offer superb surface protection and substantial lubrication and can perform well even under the most trying conditions.
A well-performing machinery experiences marginal maintenance and downtime, together with a rise in productivity. This results in zero losses, higher output, and substantial profit.
Here is a quick glance at some of the Caltex Products used in Power Gen Applications!
Steam turbine
For steam turbine equipment, it is seen that upto 1400MW per turbine is generated and is today still most common to generate the bulk of industry and household electricity. These plants are typically owned by State Utility companies and lubricants are purchased on a tender cycle. Coal fired plants will be replaced by more environmentally friendly technologies such as gas turbines and renewables. The Turbine lube oil has a life span for +10 years and oil sumps range from 20-30KL in capacity.
The pain points that steam turbines face include: water ingress, reduced oil life; unplanned downtime; aeration and poor demulsability and cavitation with root causes consisting of leaking seals, high contamination, air entrainment and its impact leading to reduced bearing film thickness; accelerated bearing wear; sludge and faster oil degradation; shorter oil drain intervals; higher operating costs.
The solutions for steam turbine include: LubeWatch 3 tier programs; Advisory support ranging from plant audits, contamination control, reliability maintenance solutions to tribology training.
Gas Turbine
For Gas turbine, it is observed that upto 500MW per turbine is generated and also are very common in the Oil & Gas segment. Meanwhile, gas fired power plants are growing as a transitional option to replace coal until newer and reliable technologies are in place. Whilst the lube oil tank capacity is smaller at 3-5KL, the oil is typically replaced every 5 years.
The problems faced by gas turbines include oxidation, varnish, overheating, unplanned downtime with the root causes being high temperatures, oil quality, poor maintenance practices and impact resulting in varnish deposits, overheating, shorter oil drain intervals, reduced power output, income loss and higher operating costs.
The solutions for Gas Turbine include: GST Advantage with varnish mitigation technology; LubeWatch 3 tier programs; and Advisory support ranging from plant audits, contamination control, reliability maintenance solutions to tribology training.
Stationary 4Stroke Gas Engine
For Stationary 4Stroke Gas Engine, it has been observed that up to 10MW per engine is generated which typically runs on Natural Gas, Biogas or Land Fill Gas from a local source.These are mostly used to power private business such as factories, Oil & Gas compression. Meanwhile, the global gas engine market is projected to have a CAGR of 5.6% with lube oil depending on the gas quality is drained every 1000-4000 Hrs and oil sumps ranging from 500-2000Litres. Due to high combustion temperatures and sulfur compounds in the gas, oil oxidation, Nitration and TBN depletion are the most common issues.
Some of the key products used for Gas Engines are HDAX 9200 SAE 40 for natural gas application; HDAX 9300 SAE 40 for natural gas application with engine using steel piston; HDAX 9500 SAE 40 for biogas / landfil gas application and HDAX 9700 SAE 40 for duel fuel engine application. Refer to Caltex sales representative for more infomation of Caltex Gas Engine Oil product application.