COOLANTS | ORGANIC ADDITIVE TECHNOLOGY
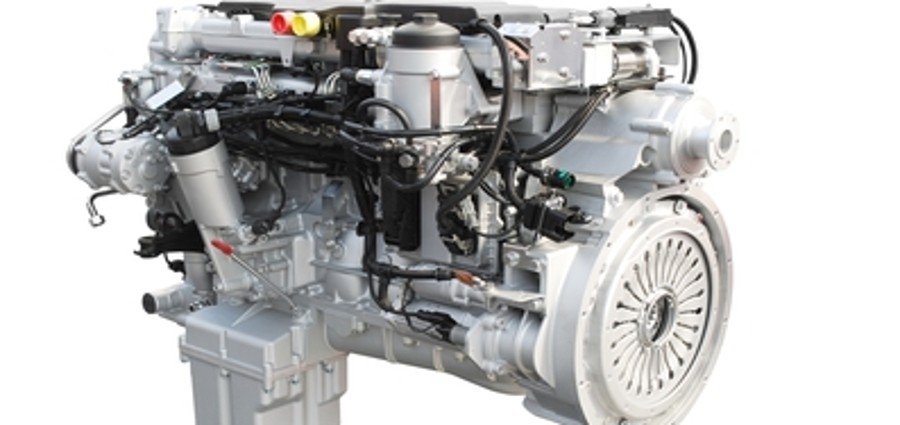
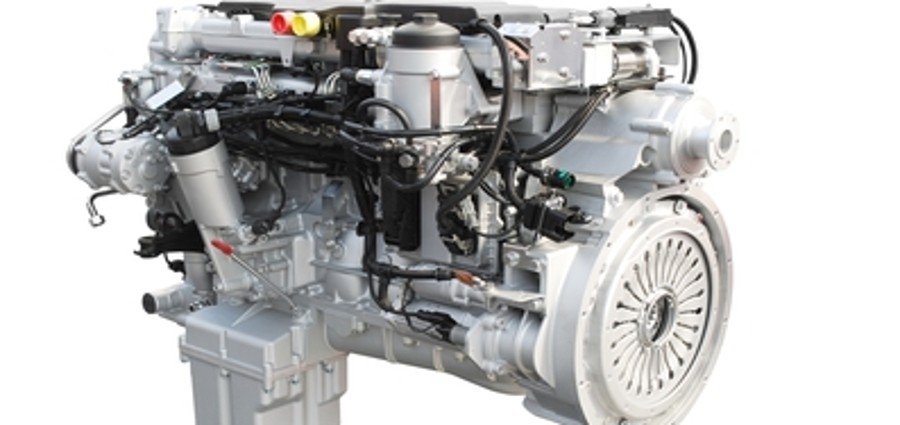
Coolants are only differentiated from each other through their inhibitor additives and their dyes. Since the dyes don’t always match the standard colour conventions, the only objective way to evaluate coolants is, then, through their additives. These additives may seem diverse, but there are really only two major types used in the world today:
- Inorganic Additive Technology (IAT)
- Organic Additive Technology (OAT)
In this post, we will look into OAT, their types, and why their chemistry has revolutionized the engine coolant industry in the last two decades.
The Older Technology
As you would have learned in the previous post, IAT coolants form a protective surface-film on the cylinder liner’s coolant side to inhibit corrosion there. What wasn’t covered in the previous post was that, in the process of forming this surface-film, the inorganic inhibitor components of the coolant—silicates, phosphates, borates, etc.—are depleted at a faster rate than is desired.
This leads to a shorter life for the coolant, and shorter service intervals, at which one is either supposed to add supplemental coolant additives (SCAs) or drain one’s cooling system and buy new coolant. The second problem is that the surface-film itself causes reduced heat exchange between the coolant and the cylinder liner, and this disorganizes the engine’s heat balance. Finally, the inorganic oxides often react with the minerals in the water to cause defective deposits that clog the cooling system—these water-based problems are intrinsic to nation, as you will find out.
The Younger Technology
OAT coolants, on the other hand, use carboxylic acids as the main inhibitors within their product. Carboxylic acids form carboxylates during the heating process, and these compounds deplete far more slowly compared to the inorganic counterparts, while also preventing corrosion as effectively.i
These organic components also avoid most of the problems inorganic additives fall into, per their reactivity with the minerals in the water. As such, their overwhelming advantages have made them the premier choice for most vehicles all over the world.ii
Without much further ado, here are the main types of OAT coolants:
- OAT: As mentioned, these purely use carboxylate additives to inhibit corrosion, which extends the life of the coolant superlatively. They act directly upon the metal corrosion sites, rather than forming a surface-film on the metal. They do not utilize inorganic additives, require the least maintenance, last the longest among all the types here, and are compatible in most nations. They are used in most light-duty vehicles. Refer to ASTM D3306 for industry standards in the testing of light-duty coolants like OAT.
- N-HOAT (or Nitrited OAT): This technology is a hybrid OAT (HOAT) that combines inorganic nitrites and organic carboxylic acids. Nitrites are used in heavy-duty vehicles, to assist with corrosion inhibition and cavitation. While nitrites are also depleted as quickly as the main components of IAT coolants, the organic carboxylates do most of the protection, hence N-HOAT chemistry still avoids most of the disadvantages of IAT chemistry. Refer to ASTM D6210 for industry standards in the testing of heavy-duty coolants like N-HOAT. Hybrid OATs usually require more maintenance than pure OATs due to the higher depletion rates of the inorganic additives.
- P-HOAT (or Phosphated OAT): Another hybrid, this coolant type does not function well in nations with hard water, as the phosphates react to create scaling corrosion on the inside of the cooling system—hence, these are not used in Europe, North America, or the Middle East, where hard water is prevalent. You can use this in most of Asia, where soft water is prevalent.
- Si-HOAT (or Silicated OAT): Silicated hybrids are mostly used in Europe. In Asia, especially Japan, problems with water pump seals and poor heat transfer have led to the ban of coolants containing silicate. Silicate IATs are very effective against corrosion, but deplete very quickly, and the resultant low silicate content in the IAT has negative effects on the cooling system. iiiSilicated hybrid, on the other hand, is effective for longer periods due to accompanying organic acids.iv
Frequently Asked Questions, regarding customers’ requirements of coolants for their coolant system:
Q: With all the technologies out there, how do I know which product is right for my vehicle?
A: It is preferable to consult your vehicle manual for compatibility information and Original Equipment Manufacturer (OEM) recommended coolant. Don’t pick a coolant based on price; pick it based on performance. Vehicles from specific manufacturers usually require a specific coolant formula.
Q: As long as I use the correct coolant and stay within the OEM recommended service, can I just top off coolant if it gets low? Why is testing so important?
A: There are many factors affecting coolant quality and performance over time, such as oxidation, pH, and additive depletion, to name a few. It is essential that proper coolant testing be part of any automotive engine maintenance program, and usage of the aforementioned ASTM D3306 and D6210 manuals will help you on your quest.v
Regional OEM Coolant Technology Preferences
Figure 1. Colors used in this figure represent various technologies, but actual coolant colors may vary.
i Long Life Performance of Carboxylic Acid Based Coolants (Link: https://www.jstor.org/stable/pdf/44632835.pdf?seq=1#page_scan_tab_contents)
ii The Role of Carboxylate-Based Coolants in Cast Iron Corrosion Protection (Link: https://www.sae.org/publications/technical-papers/content/2001-01-1184/)
iii The Effect of Silicate Content in Engine Coolants on the Corrosion Protection of Aluminium Heat-Rejecting Surfaces (Link: https://www.jstor.org/stable/44581254?seq=1#page_scan_tab_contents)
iv Engine Coolant Basics (Link: https://www.machinerylubrication.com/Read/841/coolant-fundamentals)
v Engine Coolants Basics and its Components (Link: https://www.fleetguard-filtrum.com/blog/engine-coolants-basics-and-its-classification/)