Understanding the cleanliness of Hydraulic Oils in marine industry
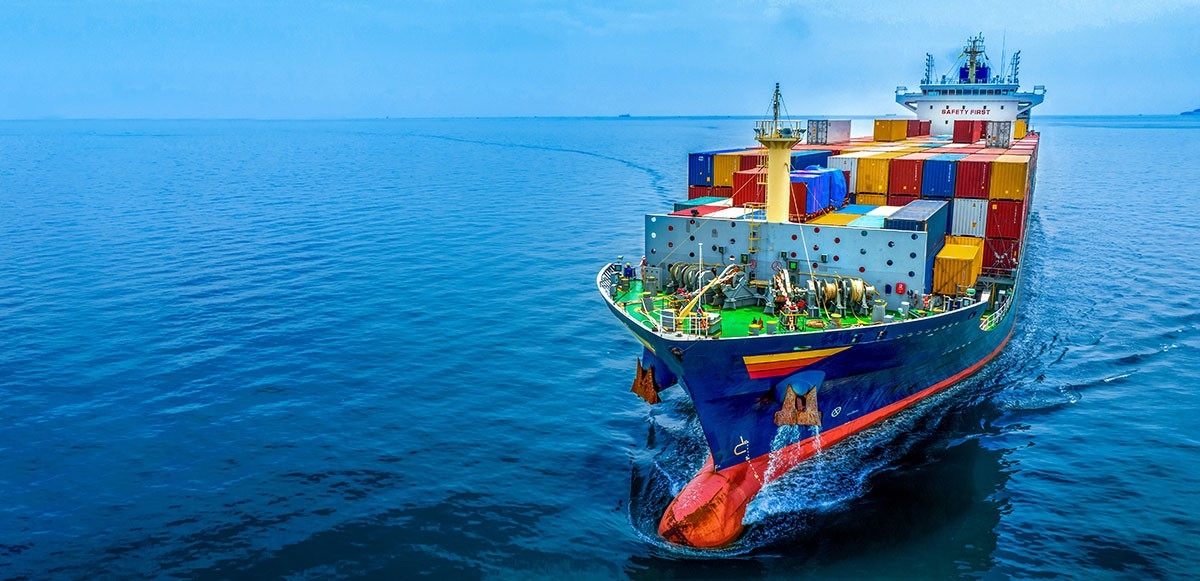
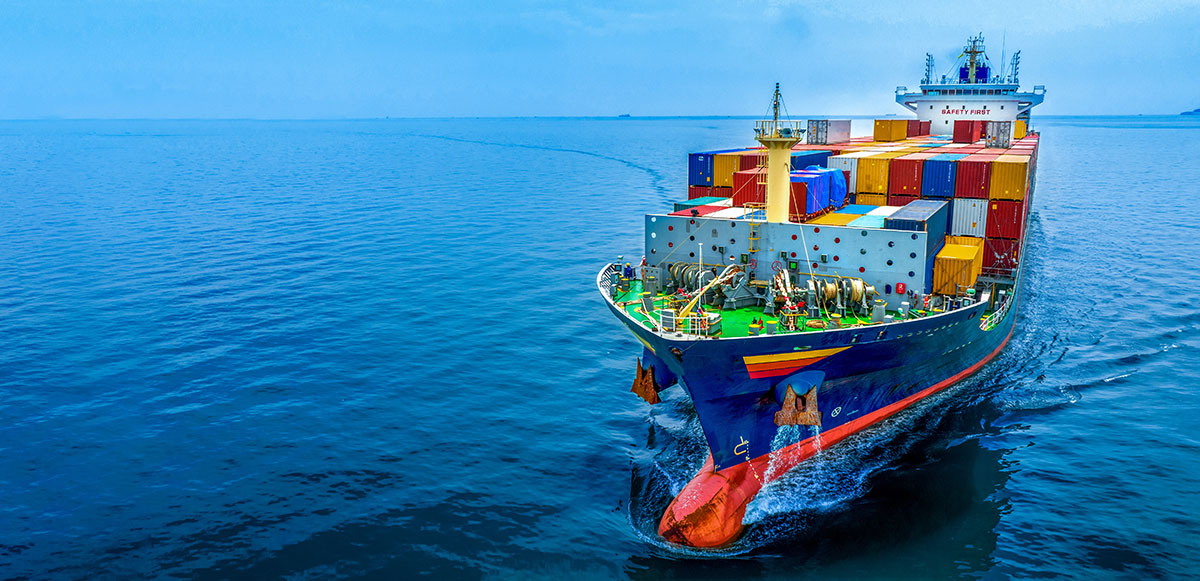
In the marine industry, most hydraulic systems onboard every vessel range from small systems for managing the engine room skylight to huge central systems to control cargo pumps, deck machinery, and steering gears.
What remains common in these systems is the hydraulic oil used to transport “fluid power”. It is important that this oil adequately lubricates the moving parts; such as the pumps, motors, and valves, present in hydraulic systems. Viscosity is one of the most critical properties of hydraulic fluids. Even though low internal friction is desirable, an oil with low viscosity at the system’s operating temperature is usually suggested. However, each hydraulic system has individual viscosity requirements based on the hydraulic pump. Other important characteristics of hydraulic oils are Oxidation Stability, Rust Prevention, Anti-wear, Air Release, Anti-foam, Low Pour Point and High Viscosity Index.
Another major factor that needs to be highlighted is the cleanliness of the oil. Taking care of the oil in the system will prevent the untimely replacement of the oil, save considerable costs, and protect the hydraulic equipment. However, selecting the proper viscosity grade is best done in cooperation with the equipment manufacturer and the lubricant supplier. Often, new systems need to be flushed before entering service to remove the system debris accumulated during construction and the oil-soluble rust preventatives applied onsite. If flushing is prescribed, it’s better to avoid taking shortcuts in the procedure because system debris may result in pump failures within a very short operating time. Additionally, oil-soluble rust preventatives negate some hydraulic oil characteristics such as foam, air release, and demulsibility properties. After commissioning, hydraulic systems also need to be checked on a regular basis for the presence of water, especially in the oil reservoir as a considerable amount of water can accumulate there from the air-breathing action that occurs at varying temperatures. Free water should be thoroughly drained to avoid the buildup of a water bottom, which can result in corrosion, sludge formation, and possibly the hydrolysis of the oil’s additive components. Also, hydraulic oils must be kept as clean as possible before and during use.
It can be safely stated that the cleaner the oil, the longer the system will function. Not only do large, hard particles cause detrimental effects, such as abrasive wear leading to pump failures, but the buildup of small, soft particles (silt) eventually results in pump wear or valve sticking. In order to avoid the buildup of particulate matter in hydraulic systems, most systems are equipped with filters to protect vital components from damage by particulate matter. Using dirty or malfunctioning filters can result in undesirable system wear. Small systems, without filters, require more frequent oil changes to avoid the buildup of particulate matter and provide prolonged equipment life.
The cleanliness of the hydraulic oils in use must be monitored on a regular basis. Large systems should be sampled once a year to oversee the oil condition and contamination level, and the basic properties to check are viscosity, water content, and amount of particulate matter. There are several methods available to establish the amount of particulate matter present in hydraulic oils: gravimetric analysis for particulate matter (filter residue), microscopic examination (sizing and counting of particles) of filter residues, and automatic particle counting in a representative oil sample.