The Role of Ash in stationary natural gas engines
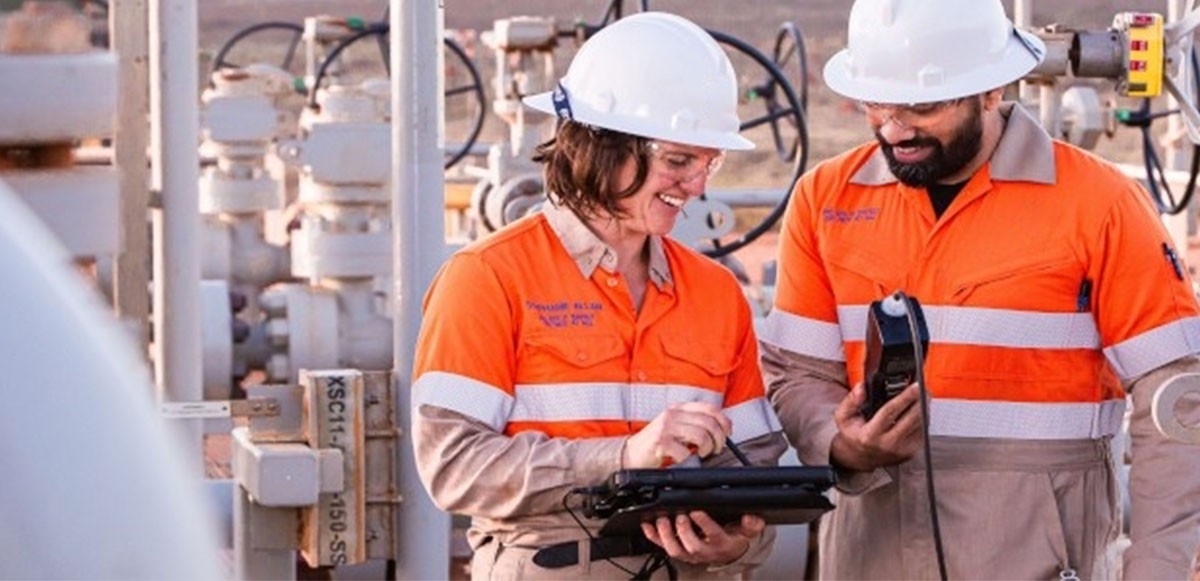
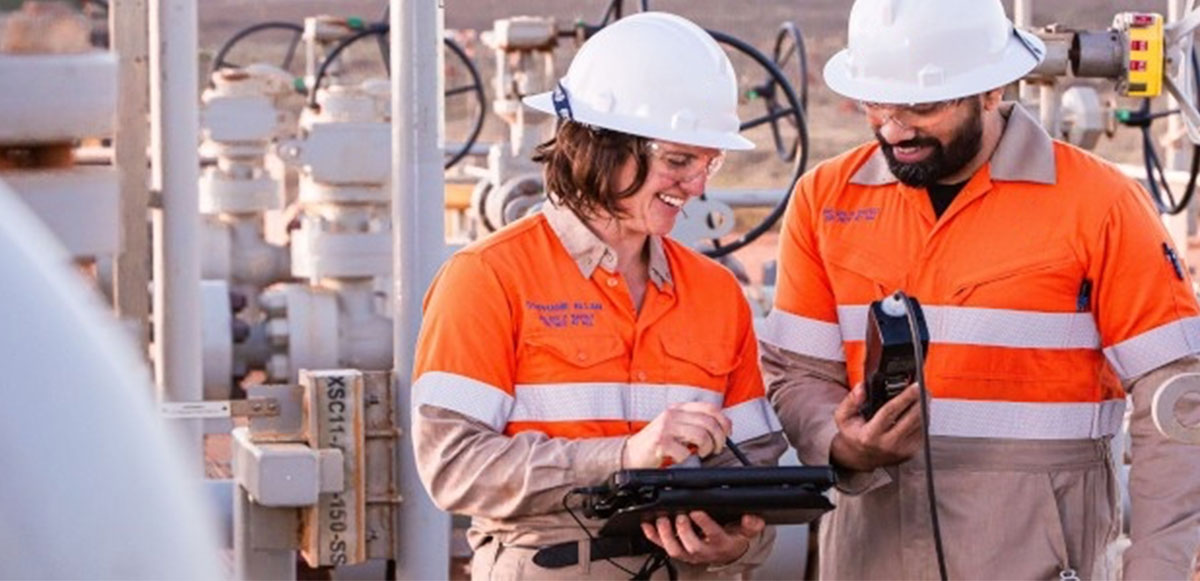
We are constantly looking at operational variables that may affect the lubrication of natural gas engines in industrial equipment. In the same context, often the level of ash content in the oil comes under scrutiny. Several questions abound. Chief among them is whether the application and operating conditions call for an ashless, low, or medium-ash oil. But that’s where the challenge arises—ash has benefits but it can also cause problems with unnecessary deposits on critical components. Therefore, it is important to understand ash’s role in the performance and durability of cylinder heads and valves in a natural gas engine’s combustion chamber, for which it is useful to understand where Ash comes from.
Ash is formed when engine oils with metallic additives (such as those containing calcium and zinc) enters the combustion chamber and burns along with the fuel. Calcium comes from detergent additives which helps neutralize acids and maintain cleanliness, while zinc comes from anti-wear additives which is effective for wear protection. As oil burns off, these non-combustible additive components remain in the form of ash, which sticks to parts of the combustion chamber. The biggest area of concern is in the valves, specifically the space between the valve seat face and the valve seat.
Some ash is desirable between the face and the seat since ash acts as a kind of cushion or solid lubricant, reducing metal-to-metal contact. What happens with too little ash is that it will lead to measurable surface wear on the face and seat, causing “valve recession” where the valve doesn’t seal properly, ultimately cutting short the life of the cylinder head. However, with too much ash collecting in this space, a portion of the cushion can break off, interfering with proper sealing between the face and the head and creating a leak path for exhaust gases. Those gases are really hot as they rush through the gap and can literally burn down or gutter the valve face. The cylinder then cannot produce any compression, and therefore, no power.
The engine load also has a huge impact on ash accumulation. What many operators don’t realize is that running the engine at partial or less than full throttle actually increases the ash buildup in the combustion chamber and on the valves, which can reduce the life of the cylinder head. It is for this reason that an ashless oil may be a more practical solution than a low ash oil, and it may even help extend the head life.
Excessive ash can also affect other parts of the combustion chamber and beyond – for example, the exhaust and aftertreatment systems. However, issues with the valves are usually the first to come to light. One rule of thumb is that two-stroke engines typically call for an ashless oil, as the smallest amounts of ash can plug up the exhaust and intake ports. However, for a four-stroke engine, a low-ash oil will do a better job of mitigating valve recession. In the end, what one needs to understand is that one needs to discuss one’s specific engine, application, and operating conditions with a lubrication expert before arriving at the optimal oil selection decision.