The Impact Of Gas Fuel Quality On Gas Engine Performance
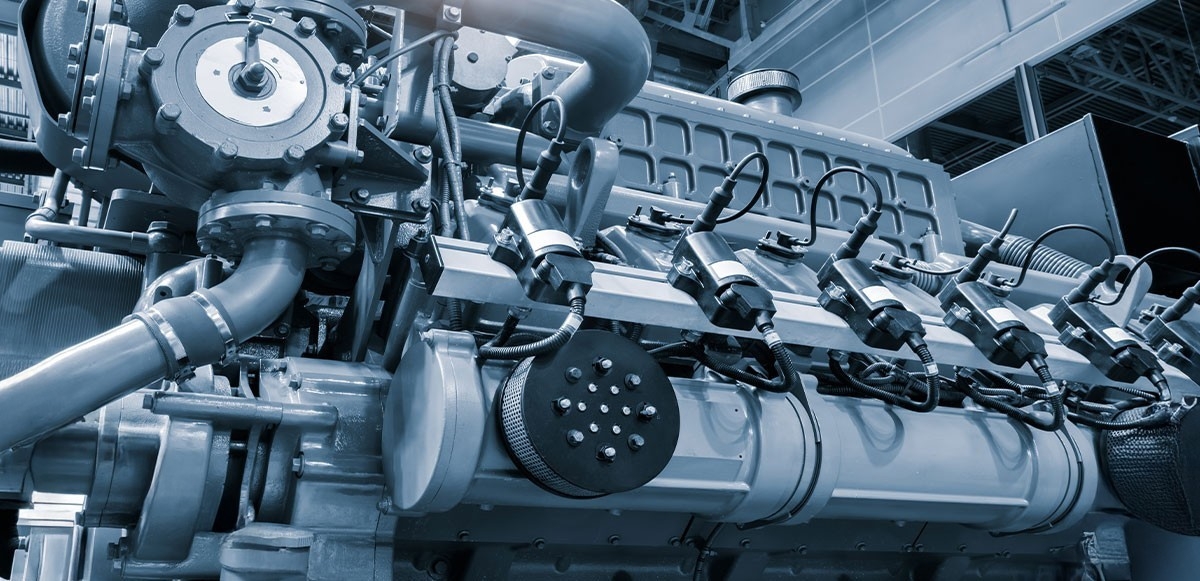
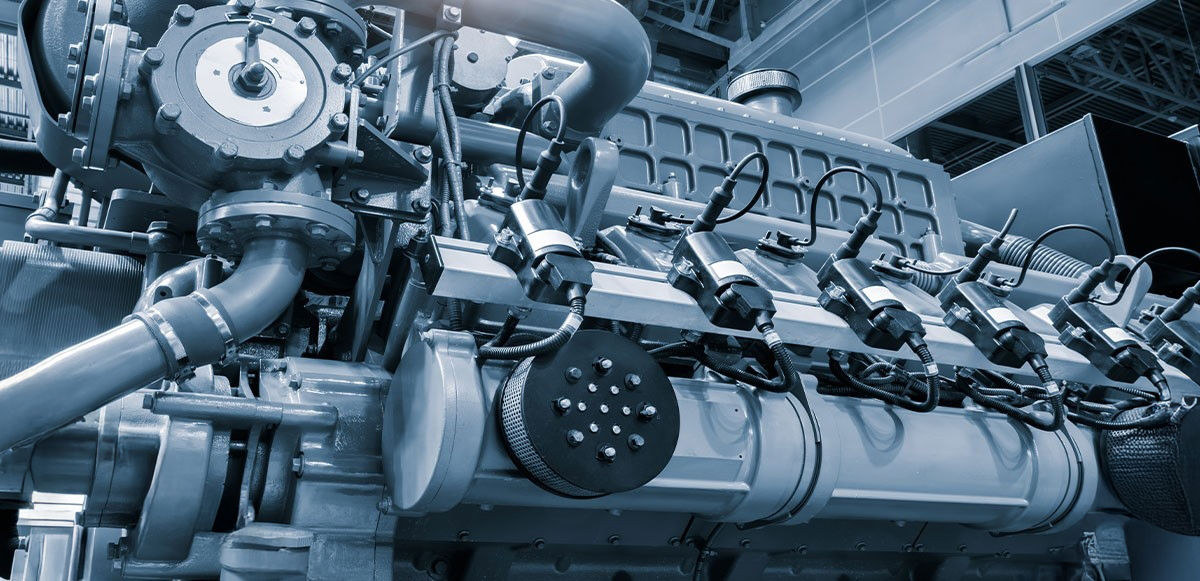
Behind the seamless performance of your gas engine lies a critical factor often overlooked—fuel quality. Just as a gourmet meal depends on premium ingredients, your gas engine relies on high-quality fuel to deliver peak performance. Whether it’s enhancing engine efficiency or avoiding costly repairs, fuel quality is the unsung hero of engine reliability. This blog explores the essence of fuel quality, how it’s measured, the consequences of low-quality fuel, and actionable tips to safeguard your engine.
WHAT YOU MUST LOOK OUT FOR
Heating Value: The heating value of natural gas determines the energy it releases upon combustion, typically measured in BTU/ft³ or MJ/m³. A higher heating value ensures better efficiency for power generation and industrial applications. It is measured using calorimeters or gas chromatography to ensure consistency in fuel quality and billing accuracy.
Chemical Composition: Natural gas primarily consists of methane (CH₄) along with other hydrocarbons like ethane, propane, and butane, as well as non-hydrocarbon gases like CO₂, N₂, and H₂S. The composition affects its energy content, combustion efficiency, and environmental impact. Gas chromatography is commonly used to analyze and ensure gas quality.
Impurities: Impurities such as hydrogen sulfide (H₂S), carbon dioxide (CO₂), and heavy metals can reduce efficiency, corrode pipelines, and increase emissions. Removing these contaminants through gas treatment processes like scrubbing and adsorption improves safety, equipment longevity, and regulatory compliance.
Moisture Content: Excess moisture in natural gas can lead to hydrate formation, pipeline blockages, and corrosion. It is measured in parts per million (ppm) or as a dew point temperature. Moisture analyzers and hygrometers help ensure gas is dry enough for safe transportation and combustion.
Pressure and Flow Characteristics: Maintaining optimal gas pressure and flow rates is crucial for transportation, storage, and end-use efficiency. Low pressure can indicate leaks, while high pressure can stress pipelines. Pressure transducers and flow meters monitor these factors to ensure stable supply and operational safety.
Wobbe Index: The Wobbe Index measures the interchangeability of natural gas based on its heating value and specific gravity. It ensures consistent combustion performance across different gas sources, preventing issues like flame instability. It is calculated using gas analyzers and chromatographs.
Density & Specific Gravity: Natural gas density and specific gravity affect pipeline flow rates and metering accuracy. A lower specific gravity means the gas is lighter than air, impacting its transport and combustion properties. Densitometers and chromatographs help measure and regulate these values.
Sulfur Content: Sulfur in natural gas, mainly in the form of hydrogen sulfide (H₂S), can cause corrosion and environmental hazards. Regulations limit sulfur content to prevent toxicity and equipment damage. Detection methods include lead acetate tests and UV fluorescence analyzers for accurate monitoring.
HOW GAS QUALITY IMPACTS GAS ENGINE PERFORMANCE
Variations in gaseous fuel composition – Changes in gas composition can affect the ignitability and combustion behavior of the gas. When lower-quality fuels are used, the engine controller must adjust operating parameters to prevent misfires, poor combustion, and knocking. These changes affect exhaust emissions, peak cylinder pressure, and knock margin. High-frequency fluctuations can destabilize engine load control, while even low-frequency variations impact diagnostics, efficiency, emissions, and optimal performance.
Variations in heating value - Engine control systems are designed for specific fuel heating values. Deviations from these values present challenges. A higher than specified heating value can result in over-fueling, requiring excessive control adjustments and potentially limiting stable operation, especially at low loads. Conversely, a lower than specified heating value can reduce load response and may prevent the engine from achieving its rated power output.
Variations in methane number - The Methane Number is crucial for optimizing engine performance, as it determines the fuel's knock resistance and influences engine setup. Fluctuations in the Methane Number alter the engine’s operating range, causing deviations from optimal performance. These variations can impact both the knock margin and ignition capability, affecting overall efficiency and stability. Methane Number (MN) is crucial for engine performance, as it measures a fuel's resistance to knock, similar to the Octane Number in gasoline. During combustion, increasing pressure and temperature can cause auto-ignition (knock), leading to performance loss and engine damage. Natural gas, with a high knock resistance (Octane ~130), enables efficient, low-emission operation. However, lower MN fuels force engines to operate below optimal efficiency, reducing power density and increasing emissions.
Variations in sulfur content - When the gas supplied to an engine contains sulfur, it's released as SO2 in the exhaust. Sulfur can be naturally present or added for safety. Beyond emissions, the acids formed from sulfur can corrode engine components, degrade lubricating oil, and negatively impact after-treatment devices such as oxygen sensors, catalytic converters, and heat recovery systems. Higher sulfur levels exacerbate these issues, leading to increased emissions, shorter equipment life, and greater operating expenses.
BEST PRACTICES TO ENSURE OPTIMUM GAS QUALITY
Understand Gas Quality Parameters - Know the acceptable ranges for heating value, methane number, composition, and impurities to ensure optimal equipment performance.
Monitor and Test Regularly - Implement routine gas sampling and analysis, using online analyzers and lab tests, to track quality and identify potential issues.
Treat and Condition the Gas - Use filtration, dehydration, desulfurization, and other methods to remove impurities and adjust gas composition as needed.
Collaborate and Communicate - Work closely with gas suppliers, share data with stakeholders, and stay informed about industry best practices.
Consider Application-Specific Needs - Tailor gas quality management strategies to the specific requirements of engines, boilers, pipelines, or other applications.
Utilize Emerging Technologies - Explore advanced gas analyzers and smart monitoring systems for more efficient and accurate gas quality management.
In conclusion, ensuring optimal gas fuel quality is paramount for maximizing gas engine performance, longevity, and environmental responsibility. By understanding the critical parameters that define gas quality and proactively addressing potential issues, operators can unlock the full potential of their engines. A commitment to consistent monitoring, proactive treatment, and collaborative partnerships across the gas supply chain is essential. This holistic approach not only safeguards valuable equipment from premature wear and tear but also contributes to a more sustainable energy landscape by minimizing emissions and maximizing resource utilization. Ultimately, prioritizing gas quality is an investment in both operational excellence and a cleaner future.