Six Tips for Choosing Hydraulic Oil of Optimal Quality
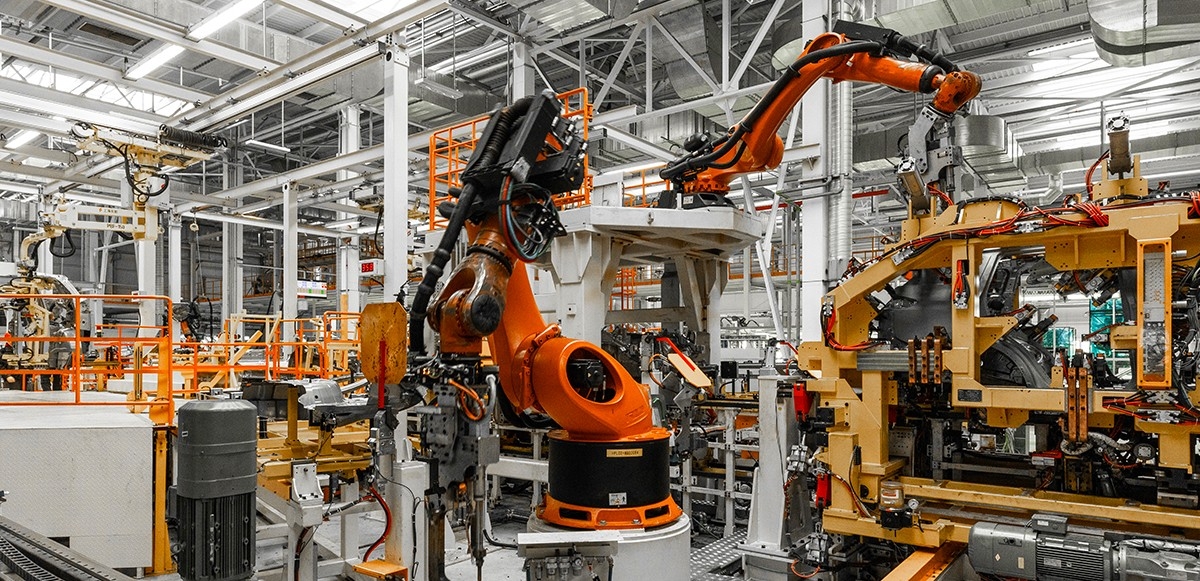
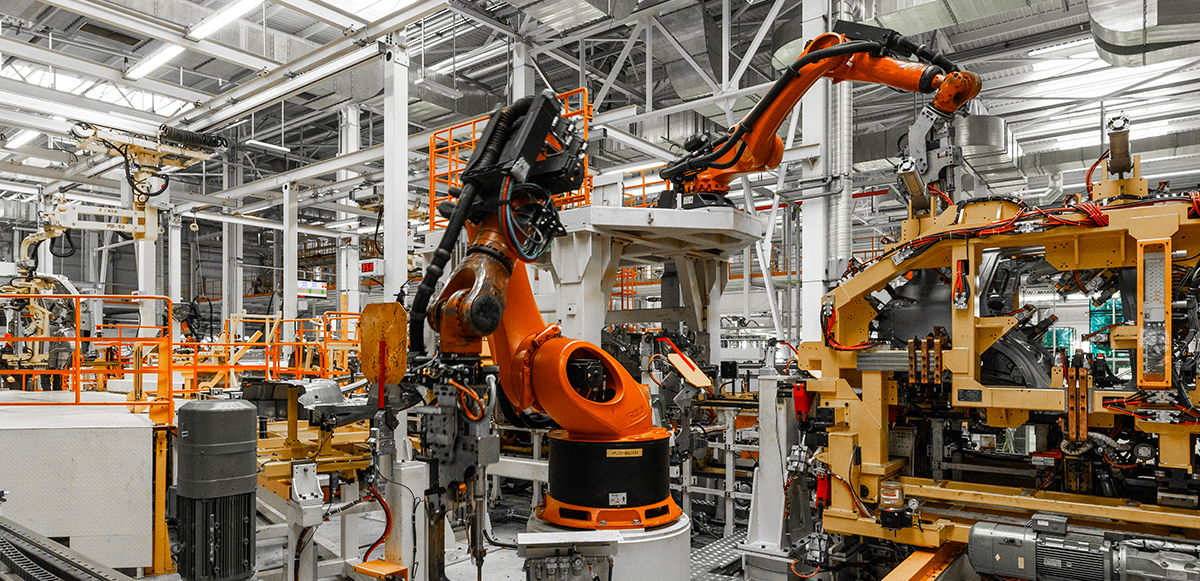
Prioritize a quality lubricant with a significant in-service lifespan and the ability to protect equipment from contamination and total system failure.
Best-performing hydraulic oils are of paramount importance for industrial plants and organizations of all kinds to ensure maximum machine efficiency and reduce the total cost of ownership for their assets. And these organizations are on the lookout for quality lubricants, but most often they tend to be clueless. A checklist would be useful. Among the many features they must look for, they must prioritize a quality lubricant with a substantial in-service lifespan and the ability to protect equipment from contamination and total system failure.
Here are six tips to help you choose hydraulic oil of optimal quality:
- Use a Turbine Oil Oxidation Stability Test (TOST) to evaluate the potential service life of hydraulic oils but refrain from only using the TOST to give you a whole picture. Test conditions may not reflect real-world conditions, so consider other tests and properties when selecting a hydraulic oil.
- It is very important to use the TOST test results in conjunction with key performance indicators such as wear resistance, viscosity, oxidation stability, and zinc levels to uncover the true useful life of hydraulic oils.
- Always ensure the chosen hydraulic oil offers excellent wear resistance since severe wear, although controllable, is a significant issue. By picking a hydraulic oil that best protects machines in a facility’s environment, plants will certainly extend their savings by reducing unexpected manpower and monetary expenditures that may crop up in the future.
- Being aware of the fluid’s viscosity, a measure of a fluid’s resistance to flow and shear, is reportedly one of the oil’s most significant physical properties. It’s important to be aware that viscosity, both too high and too low, can cause serious damage to a system, which is why it's essential to strike a balance between a machine’s requirements and its environmental demands.
- Checking oxidation stability is crucial. The hydraulic oil’s capability to withstand heat-induced degradation is a result of a chemical reaction with oxygen. It is flagged by a foul odor, an increase in viscosity, and a darkening of the oil. Conditions such as high temperatures, water, acids, and other catalysts such as copper affect the rate of oxidation. Always closely evaluate the base stock and the antioxidant package of a lubricant, as this helps facilities better understand an oil’s ability to protect itself and provide maximum service life.
- Understanding zinc levels is important. For years, zinc has been a central additive in hydraulic oils for its antioxidant properties. It is mainly used as an anti-wear agent or an antioxidant. ZDDP or zinc dialkyl dithiophosphate, uses phenolic and aminic compounds to weaken free radicals and disengage the oxidation reactions, hindering harmful acidic byproducts from corroding equipment parts or changing the base oil’s lubricating capabilities. Despite this plus point, using zinc-based additives can have serious outcomes. ZDDP compounds vary greatly in their effects on hydrolysis and thermal degradation, making it hard for lubrication manufacturers to obtain high-quality levels.