Oil Analysis: Keeping Off-highway Equipment Running Optimally In Critical Conditions
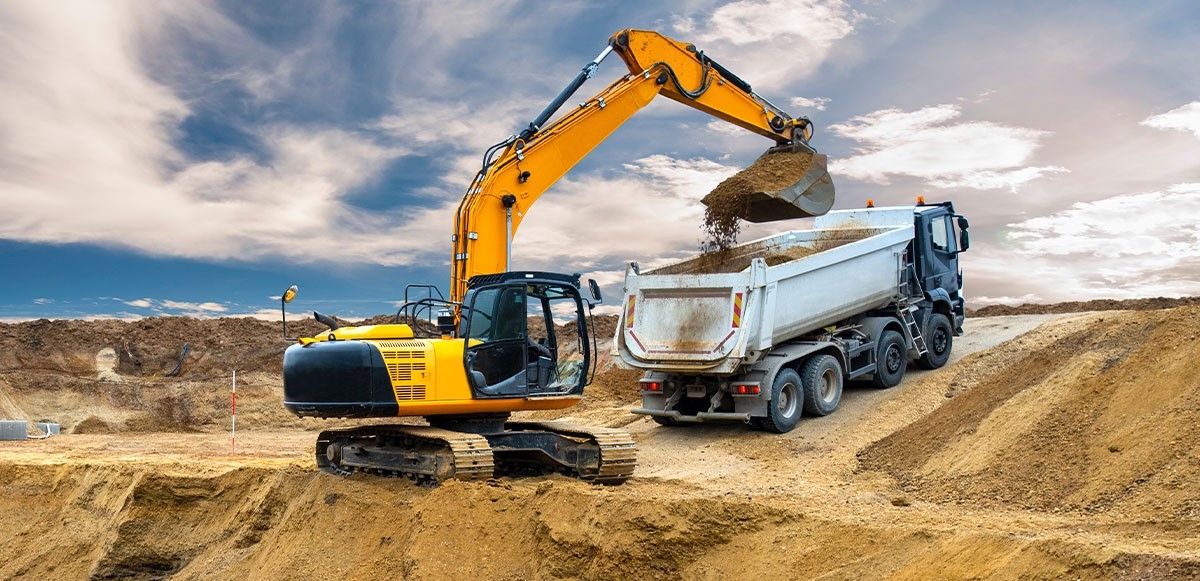
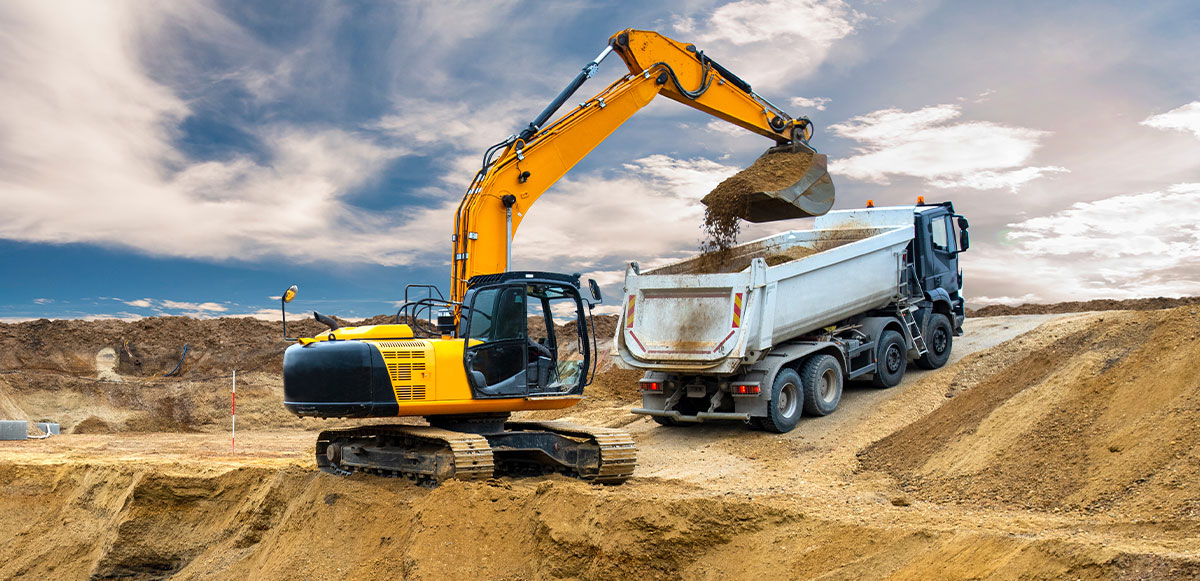
Heavy equipment requires heavy investment and heavy maintenance. It is the most critical part of your operations and it is imperative to take good care of it to ensure value return on investment.
Off-highway equipment like agricultural, mining and construction equipment including wheel loaders, forklifts, excavators, bulldozers, crawler loaders, motor graders, scrapers and tractors have different lifespans ranging from 7,000 – 12,000 hours (wheel loader), 10,000 hours (forklift), 9,800 hours (excavator), 7 – 10 years (bull dozer), 3,500 hours (backhoe loaders), 25,000 hours (scrapers), 12,000 hours (motor graders) and 20,000 hours (crawler loaders) and 4,000 hours (tractors).
However, this equipment battles the harshest of conditions ranging from inclement weather and operating conditions, overuse and storage issues like exposure to moisture. If left unchecked, these issues can affect your equipment, halting operations in a heartbeat.
Therefore, it is necessary to routinely test and practice predictive maintenance. A major part of this is monitoring all fluids associated with the asset. This in-service analysis helps identify contaminants, abrasives, oxidation, dilution, leakage, soot and more. It also helps extend the equipment’s lifespan and save on cost and time.
Let’s understand the properties of some fluids generally used in major components of the asset.
Engine oil:
Checking the viscosity, wear metals, oxidation, and contamination can help avoid unplanned vehicle breakdown and unnecessary expenditure to ensure optimal operation efficiency. By monitoring machine wear and oil degradation, it helps to provide a clear picture of present and potential issues that may arise this give operators a chance to prevent future engine operation failures.
Coolant:Heavy equipment typically has a lifespan of about 5 years or 1200 – 1500 hours. Coolant which requires to cool engines are exposed to elevated temperatures. Overtime, coolant is expected to deteriorate beside exposure to elevated temperature it also had to subjected to oxygen, dirt, debris and corrosion. This can lead to overheating, and damage to components, pushing the equipment towards unplanned breakdown. To avoid this, it is imperative to conduct routine inspections, schedule replacements and address leaks.
Hydraulic fluid:
The most common issues that hydraulic fluids face are entrapped air and water along with dirt, rubber or metal particles and deterioration due to high operating temperatures. With a lifespan of 2,000 – 3,000 hours, it is important that this fluid be maintained and changed regularly to prevent costly repairs.
Apart from the assessment, the LubeWatch Oil Analysis Program also helps you track the performance of fleet vehicles and equipment that is the lifeblood of your business. The benefits of the program speak for themselves with 80% users reporting it helped maximize their equipment uptime, 69% reporting that the analysis test results helped them optimize drain intervals up to two times of the standard drain and 80% reported that scheduled downtime saved them more money compared to the cost of unexpected component or equipment failure.
Regular oil and fluid analysis informs you of impending problems your equipment can face. Scheduling repairs via this method helps avoid having too many repairs thus helping you save money, ascertain the fluid’s remaining useful life, identify and do away with contaminants and help enhance the life of the fluid and health of the machine.