In-Service Oil Analysis – What, Why And How
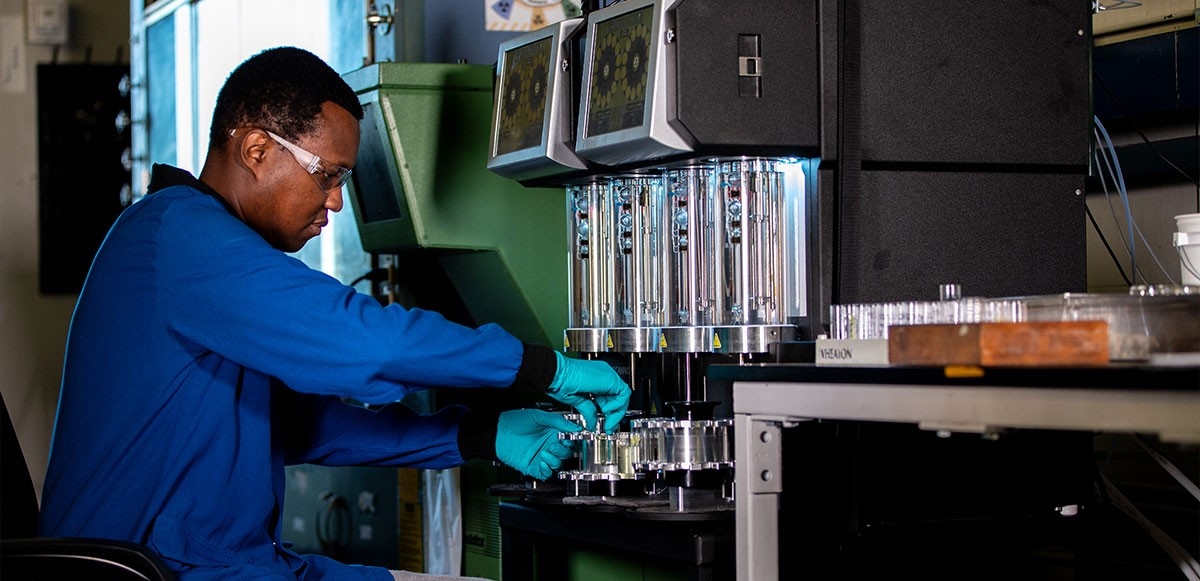
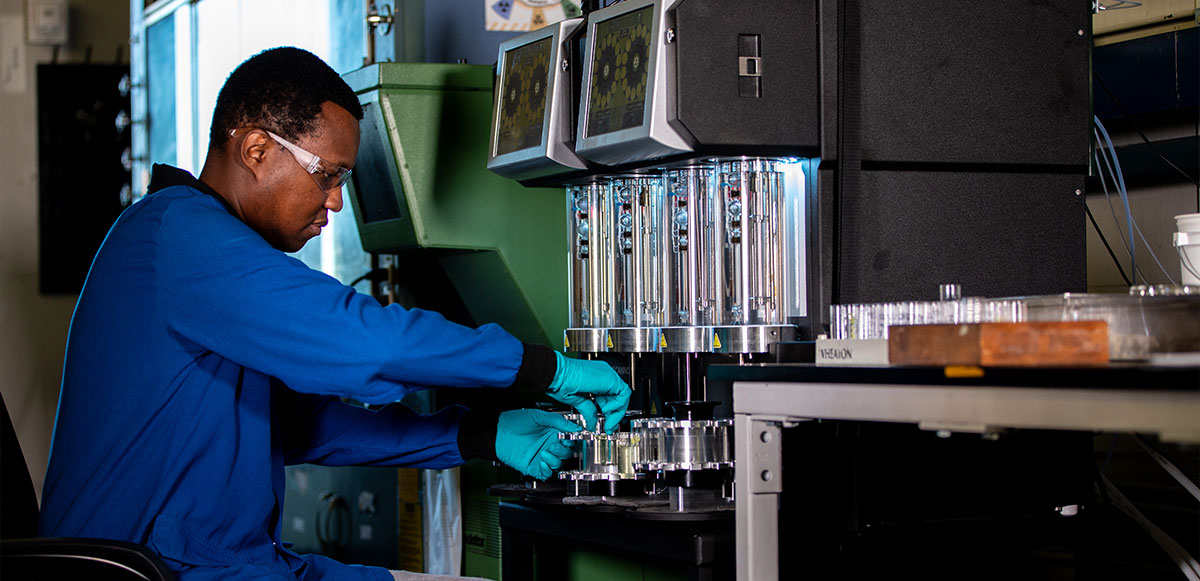
The Importance of In-Service Oil Analysis: Protecting Your Equipment
What started as a practice on locomotive engines over a century ago has now become an irreplaceable part of equipment maintenance. In-service oil monitoring is part of condition- based maintenance to gather data on lubricant / oil health to determine maintenance schedules. Lubricants are the lifeblood of industrial machinery and it is imperative to analyze these fluids for contamination to prevent billions of dollars in repair or maintenance, improving performance and reliability.
Understanding Oil Contamination Contamination is a major culprit in lubricant degradation. It can come from various sources:
Solid contaminants:
These include dirt, dust, metal wear particles, and combustion by-products. They can enter the system through seals, vents, or inadequate filtration.
Liquid contaminants:
Water, fuel, or coolant can find their way into the lubricant, leading to corrosion, emulsion formation, and decreased lubricant performance. Condensation too, due to temperature changes between day and night or between equipment operation and shut off, can get water into the system and increase the risk of wear.
Gaseous contaminants:
Air, combustion gases, or other vapors can dissolve in the oil, altering its properties and leading to oxidation.
Varnish:
High-operating temperatures and oxidation can cause the formation of varnish, which degrades the effectiveness of the lubricant and, in combination with particulate matter, can create abrasive surfaces within the equipment. Across different assets, one common contaminant is the accidental use of an incorrect lubricant while topping off old oil.
The Role of Oil Analysis
Oil analysis is a diagnostic tool that examines the condition of the lubricant in service. It involves a series of tests to assess various parameters, including:
Viscosity:
Measures the oil's resistance to flow. Changes in viscosity can indicate degradation, oxidation or contamination.
Contaminants:
Identifies the presence and quantity of solid and liquid contaminants, helping to pinpoint the source of contamination.
Wear metals:
Analyzes the concentration of metal particles to detect abnormal wear in machine components.
Additives:
Evaluates the depletion of essential additives that provide specific performance properties.
Oxidation and nitration:
Measures the degree of oil degradation due to exposure to heat and oxygen.
The Benefits of In-Service Oil Analysis
Regular oil analysis offers numerous advantages:
Early detection of problems:
By identifying issues before they escalate, you can prevent costly equipment failures and downtime.
Optimized maintenance:
Oil analysis helps determine optimal oil change intervals, reducing waste and costs.
Extended equipment life:
Early detection of wear and contamination allows for corrective actions, prolonging the lifespan of machinery.
Improved reliability:
By maintaining lubricant quality, you enhance the overall reliability of your equipment.
Predictive maintenance:
Oil analysis enables a proactive approach to maintenance, shifting from reactive repairs to planned interventions.
Cost savings:
Early detection of problems prevents costly repairs and reduces overall maintenance expenses.
Implementing an Oil Analysis Program
To maximize the benefits of oil analysis, it's essential to establish a systematic program. This includes:
Selecting appropriate tests:
Determine the specific tests required based on equipment type, operating conditions, and potential failure modes. For solid contamination like particles, best-practice monitoring involves sampling oil at regular intervals and sending them to a lab for particle count testing. A simple test you can perform at your facility is a patch test, in which an oil sample is run through a filter membrane and observed through a microscope. Commercial patch test kits are widely available. For water contamination, a “crackle” test conducted by a lab is an easy check. In this method, oil is placed on a hot plate and if it starts to bubble and pop, it means moisture is present in the oil. The more-involved Karl Fischer titration test will quantify the percentage or parts per million of water present. To check the presence of varnish, the standard ASTM-approved way to test is the Membrane Patch Colorimetry or MPC Test. This is usually a lab test but can be performed using MPC test kits for onsite testing.
Establishing sampling points:
Identify optimal locations for oil sampling to accurately represent the lubricant's condition.
Developing a sampling schedule:
Determine the frequency of oil analysis based on equipment criticality and operating conditions.
Analyzing and interpreting results:
Work with qualified professionals to analyze the data and understand its implications.
Implementing corrective actions:
Take prompt action to address any identified issues.