How to keep your hydraulic system clean to optimize equipment performance
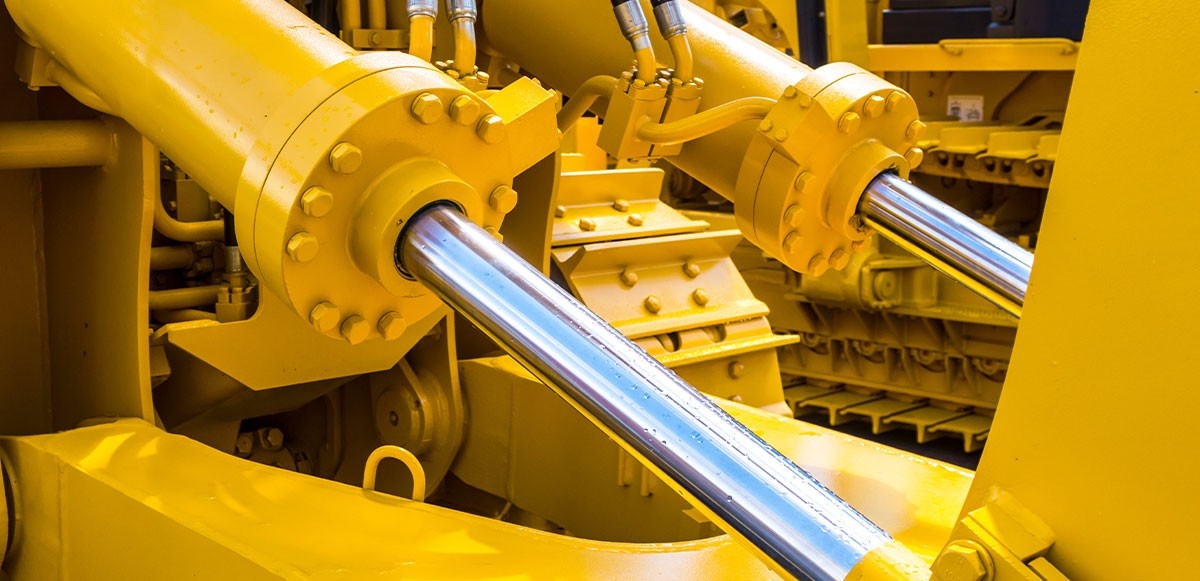
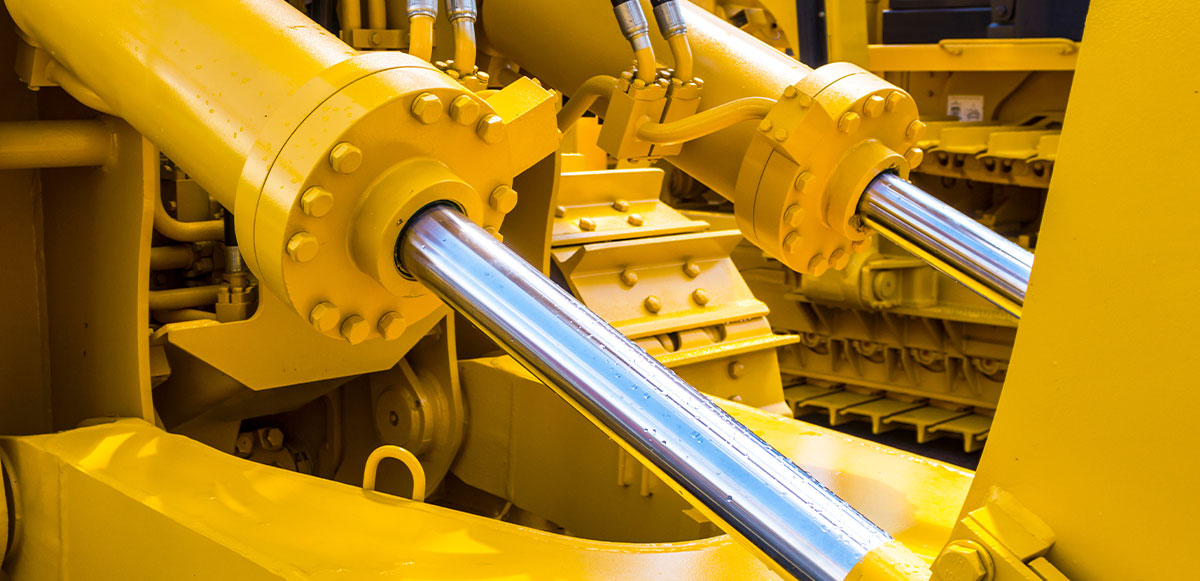
To optimize equipment performance, one has to maintain the upkeep of the hydraulic system. In this blog, learn how starting with clean oil and regular routine analysis can make a world of difference.
Clean oil has many benefits. It reduces waste mainly because the oil resists degradation longer and it may not be required to be changed as often. This way, one can avoid the cost of a new lubricant as well as the disposal of the old lubricant. With clean oil, one also notices a decrease in the requirement to change filters frequently.
Often one notices reduced energy consumption since dirty sticking valves need more force to move, using more fuel or electricity.
Also, keeping your hydraulic system clean will extend equipment life by tenfold, mainly by removing abrasive particles that contaminate moving parts. This is crucial since over the last few years it has been observed that a lack of readily available parts causes extended downtime when breakdowns occur.
An overlooked factor is that equipment is often operated in dirty, dusty, humid environments, Also, lubricants are also exposed to contamination during the process of multiple delivery transfers. Therefore, while the oil that leaves the refinery is clean, by the time it is delivered, it reaches a contamination level that is well over the specified OEM cleanliness for most equipment.
Ways to keep your hydraulic system in mint condition
- Allot a Program Champion for your oil analysis program – one person who is responsible for your analysis program.
- Regularly, take samples for oil analysis to track cleanliness levels while ensuring targets are being met.
- Track and document your contamination control successes, including any savings achieved though proactive maintenance and fix-before-failure.
- Ensure your team’s wins are recognized and acknowledged within your company’s internal communication to encourage buy-in amongst your team.
Also, install the appropriate filters for your equipment. At the onset, keep OEM’s specifications in mind along with the environment’s severity. Vent plugs can allow dirt and moisture to enter so it’s important to replace those with desiccant breathers as well.
Finally, consider using a program like LubeWatch oil analysis. This program helps one to track the performance of the lubricants in your equipment. By analyzing oil samples regularly, one can optimize equipment life and oil replacement intervals, identify lubricant-related needs and understand the changing environment within a piece of equipment. This aids in the clear-cut scheduling of maintenance work that can reduce downtime or even remove the risk of catastrophic failure.
Utilizing some of these tips for ensuring the use of clean hydraulic oils from the start can help avoid harmful contamination, unplanned downtime and costly maintenance repairs.
In conclusion, starting with clean oil and performing routine analysis can result in optimized equipment health, increased reliability and steady production.