When Must You Perform a Lubricant Contamination Control Check
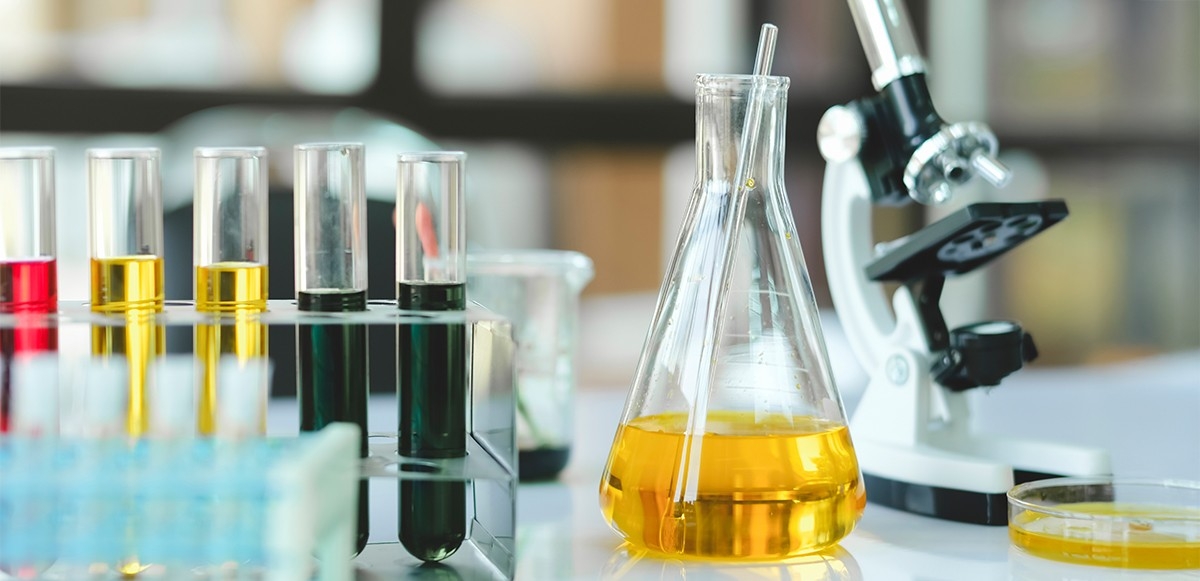
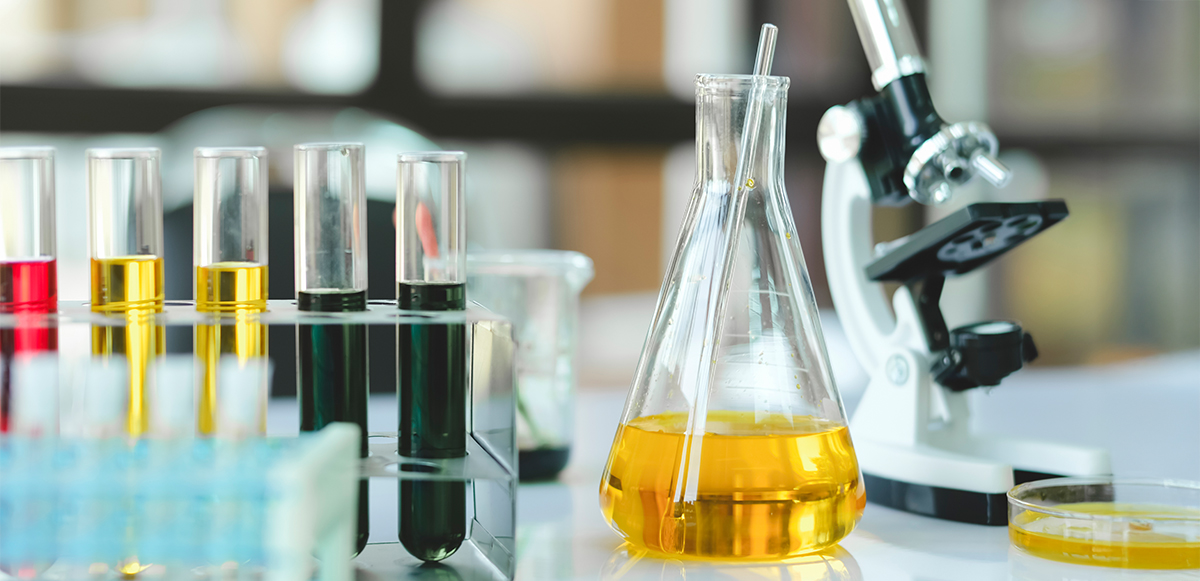
Just like good hygiene plays an important role in a healthy lifestyle, good quality lubricants play an important role in the smooth operation of industrial machinery. Lubricant contamination is one of the leading causes of lubricant failure, resulting in equipment damage, downtime and increased maintenance costs. Studies in the related industries of machine reliability and tribology reveal that 70 – 80% of machinery failures can be attributed to lubricant contamination.
The Cost of Lubricant Testing
The 70 – 80% we mentioned above takes up approximately 1 – 3% of the total maintenance budget. Not a big number when you glance at it, but it can put a dent in your budget over time.
This brings us to the question, how exactly do lubricants get contaminated and how do we prevent that from happening?
While we may be aware of lubricant contamination during machinery operation, we assume that new oil equals clean oil. However, that is not the case. Contamination can occur either during production or storage or transportation due to fluctuations in temperatures across locations, exposure to sunlight, dirt, dust and moisture among other weather-related conditions. Let’s understand how.
The Three Key Checkpoints for Lubricant Testing
1. Production: Lubricants are a mix of base oils and additives. In case of grease, thickeners are added as per intended use. This process of production requires blending in a specific type of mixing equipment in a specific atmospheric setting. However, a few problem areas can crop up here. For example:
a. Cleanliness and sanitation of the blending container.
b. Whether or not the air used is moisture-free.
c. Whether or not components have undergone filtrationd. Whether or not the blending container has a breather mechanism.
2. Storage: After production, lubricants are generally stored in large reservoirs before distribution. And while new storage containers are either designed based on volume, it is mostly old containers that are repurposed for use. This stage too is not devoid of problems. For example:
a. Presence of welding or other residue on the inside of containers.
b. Not up-to-the-mark cleanliness of previously used containers.
c. Improperly installed breathers on tanks that lead to infiltration of particles or moisture.
d. Not filtering lubricants before transfer.
3. Transportation: Lubricants are transported in bulk tankers, drums, or totes to their final destinations. Improper handling, exposure to environmental elements, and inadequate cleanliness protocols during transit can lead to contamination. For example:
a. The materials used to make containers for specific oils can lead to contamination.
b. The use of non-dedicated containers or mixing containers can lead to cross contamination.
c. Open pipe connectors and couplers, allowing contaminants to enter during handling.
d. Tanks are cleaned either using steam or diesel fuel and insufficient flushing of previously used tanks or drums, carrying over residues from past shipments.
How and When to Perform Checks for Lubricant Contamination
Let’s explore simple quality checks you can implement onsite to ensure lubricant reliability and decrease contamination.
1. Inspect the lubricant container: Conduct a visual check for breather and label conditions. Check if the labels on the barrels are clean, intact, not torn, broken or misprinted. Maintain a checklist to record the label condition.
2. Ask for the test certificate: Lubricant test certificates contain detailed information about the quality of the lubricant before dispatch like oil analysis, details of the test, results, etc. Ask for this when you are supplied with the lubricants.
3. Perform a basic oil analysis: Conduct bottle sampling and patch testing to detect contaminants introduced during transportation.
4. Undertake oil filtration: Adopt inline filtration of bulk deliveries before adding to storage tanks or machinery. Installation of a mechanical filtration room within the facility is advised to initiate the process of filtration. This is to ensure that any solid particles or moisture are removed before oil use. When transitioning between different oil grades, having a dedicated machine for this purpose is crucial to conducting a thorough flushing procedure.
5. Appropriate lubricant storage: Minimize outdoor storage. Create appropriate indoor warehousing with concrete walls and roof, a slip-resistant or epoxy floor, ventilation, boundaries for a workspace, sealed climate control setup, informative displays, dedicated equipment for lubricant handling, safety gear and practices to keep dirt and dust out of the setup.
These checks make for proactive preventive maintenance strategies. Let’s reiterate.
1. Implement advanced filtration systems to remove particulate and moisture contamination.
2. Use desiccant breathers to prevent moisture ingress in storage containers.
3. Train personnel on proper handling and storage procedures to minimize human errors.
4. Set up scheduled maintenance programs to replace and analyze lubricants at optimal intervals.
5. Label and color-code lubricants to prevent misapplication and cross-contamination.
6. Seal storage and dispensing systems to prevent airborne contaminants from entering the lubricants.
7. Control environmental conditions, such as humidity and temperature, in storage areas.
While you do your best in implementing these preventive maintenance strategies, contamination can still occur due to human error, malfunction or accidents. Hence, it is always advisable to have mitigation strategies in place to minimize damage, save on costs and ensure quick restoration of lubricant quality and machinery operation.
Some mitigation strategies include:
1. Conducting a root cause analysis to identify and address contamination sources.
2. Immediate filtration and oil purification to remove contaminants before they cause damage.
3. Replacing severely contaminated lubricants to prevent further harm to machinery.
4. Reviewing and reinforcing preventive measures to reduce the likelihood of recurrence.
5. Flushing the lubrication system if contamination has affected internal components.
6. Increasing the frequency of monitoring in high-risk environments to detect contamination early.
In addition to the preventive measures discussed, partnering with experts can further enhance your lubrication management strategy. The Caltex LubeWatch® Oil Analysis Program offers advanced diagnostic and preventive maintenance testing designed to evaluate oil condition, component wear, and contamination across various systems, including engines, hydraulics, and gearboxes.
By enrolling in the Caltex LubeWatch Oil Analysis program, you gain access to:
1. Precise Insight: Insightful oil analysis with precision diagnostics.
2. Professional Advice: Actionable recommendations from professionals based on oil analysis.
3. Punctual Reporting: Rapid and reliable lubricant testing for prompt decision-making.
Regular oil analysis through Caltex LubeWatch enables early detection of potential equipment issues, allowing for planned maintenance and reducing the risk of unexpected downtime. This proactive approach not only extends equipment life but also optimizes operational efficiency. Integrating Caltex's LubeWatch Oil Analysis Program into your maintenance routine ensures that your lubrication practices are aligned with industry best standards, providing peace of mind and contributing to the long-term success of your operations.