The Four Biggest Engine Killers
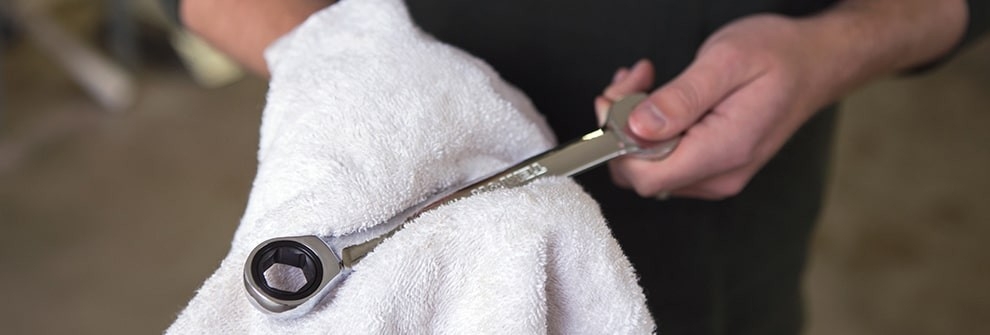
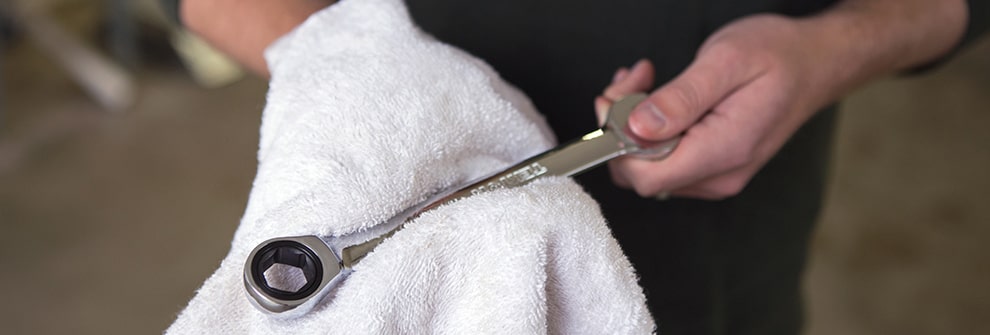
Incorporating oil analysis, a valuable preventive maintenance tool which can help identify potential problems before it leads to major repairs, as part of your long-term maintenance plan can help you as a fleet manager identify major problems that can impair engine durability and performance which can save you thousands of dollars in repair and replacement costs.
Oil analysis often points to the types and levels of contaminants in the oil as well as the possible causes of contamination. Parameters such as oil viscosity, presence of metal elements and coolant/glycol levels are some of the factors our lab conducting the analysis has looked at.
That’s why it’s important to properly maintain the lubrication and engine cooling system in order to keep the engine’s health at an optimum level. Issues such as dirt, soot, fuel dilution levels and coolant leaks threaten your engine well being.
For example, levels of silicon and aluminum, the basic components of dirt, are clear indicators of an air intake filtration leak letting dirt into the combustion chamber. High levels of chromium suggest that the resulting abrasion is wearing the chrome off the piston rings. So finding and correcting issues with your air intake system limits the abrasive damage of dirt, if left unchecked this may lead to complete failures.
Thick, sooty oil on the other hand can hinder filters, increase operating temperatures and cause harsh wear and early detection of that excess soot may identify exhaust issues. High-performance additive formulation of hydrocracked base fluids and carefully balanced metallic detergent and ashless dispersant additive system can provide superb soot dispersion and prevents deposit from building up.
Fuels with biofuel blends increase the risk of dilution in the engine oil which as a result reduces the oxidation stability that directly impacts the oil drain intervals. Therefore, identifying fuel dilution at low levels allows for correction of the issues before engine damage happens and averting them from becoming less capable of withstanding high loads at certain points, such as the rod bearings and crankshaft areas.
Oil analysis can also detect a coolant leak within the engine. Water or glycol may vaporize as soon as they leave the cooling system, but the contaminants in the coolants leave traces of sodium, potassium or boron in the oil, which are indicators of a leak.
You also have levels of silicon and aluminum, which indicate air intake filtration leak letting dirt into the combustion chamber. While high levels of chromium suggest that the resulting abrasion is wearing the chrome off the piston rings.
Armed with the right information, you can better prepare to take preventive action to protect your equipment, extend its life, minimize downtime and avoid or even eliminate replacement costs. To learn more check out: