Learning to address industry-specific coolant needs
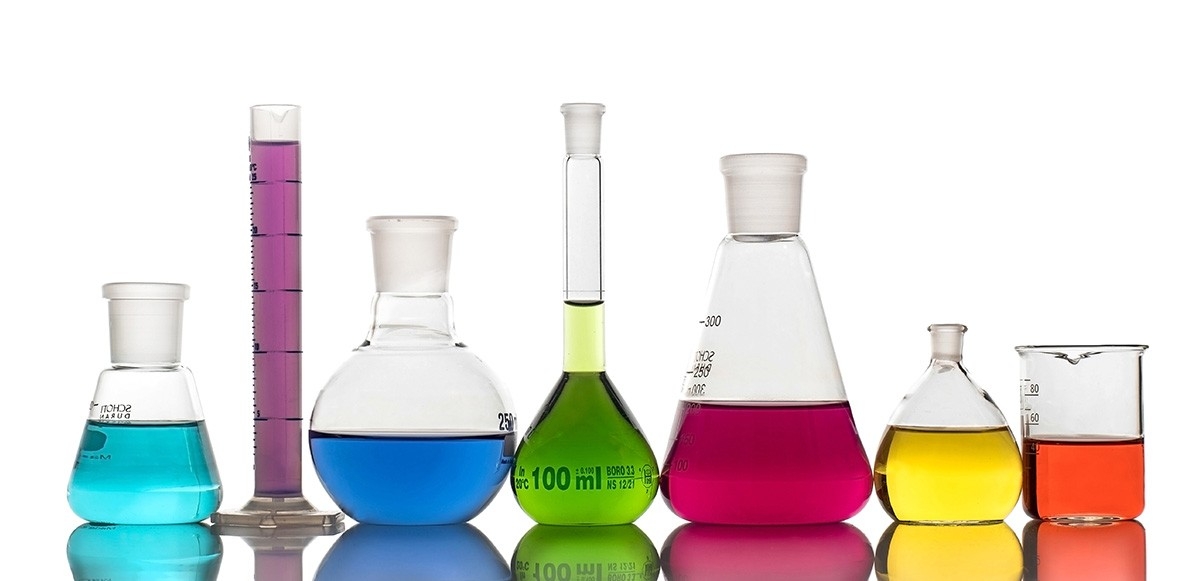
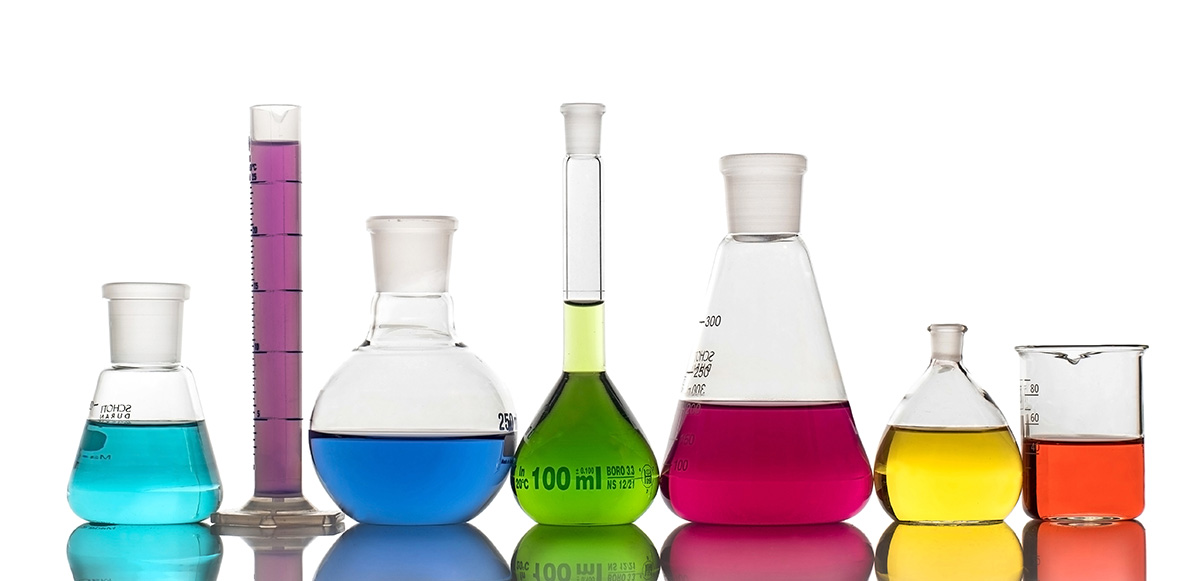
Each industry may have specific coolant concerns; the main goal is to maintain equipment and get the most out of it for as long as it is possible.
Learning to keep your engine coolant in ship shape is easy and often overlooked. The first rule of thumb is understanding the fluid and equipment needs are key to proper maintenance in the field. With proper maintenance, the fluid and equipment health can deliver sufficient functions to protect and remove heat from the component parts as necessary.
Different applications and environments can worsen potential problems that may hamper the ability of the cooling system to circulate, remove heat and then dispel the heat before circulating again through the system. For the cooling system, these functions maintain and protect the equipment.
Each industry has a specific coolant testing that can identify potential issues and/or concerns. Because fluid chemistry plays a critical role in the cooling system’s ability to transfer heat and prevent corrosion, it safeguards overall system health.
Off-Highway/Construction
In this industry, maintenance takes priority. Economic conditions and supply issues have made it necessary to extend the fleet's lifespan beyond the average lifespan of 3.5 to 4 years.
As part of an effective predictive maintenance program, monitor the below concerns:
a. High Temperature Issues
• Glycol concentration
b. Chemistry Issues
• Corrosion inhibitor
• Mixing
c. Contamination
• Scale hardness
• Glycol degradation
Manufacturing:
In this industry, higher ambient temperatures in different equipment types require different fluids to maintain system temperatures. Monitoring and knowing the fluid types are key for proper maintenance.
Common coolant system concerns to monitor include:
a. OEM Requirements and Coolant Supplier Support
• Understanding equipment recommendation for glycol to water concentrations
b. Contamination Issues
• Scale hardness
• Glycol degradation
Power Generation
The duty cycle for this industry is a ‘long term, low maintenance.’ Typically, fluids in the system are in a state of inactivity. Operating only when needed, when serviced, or when demand is required.
Common engine coolant concerns to monitor are:
a. Contamination
• Degradation acids
• Grounding concerns
• Air leak
• Scale
b. High temperature
• Glycol concentration
• Maintain proper OEM glycol to water concentration
c. Chemistry issues
• Corrosion inhibitor
• Mixing
Marine
The marine industry incorporates a wide range of engine coolant systems; these systems are often deployed with little access to repair parts or facilities for extended times. Increasing the system’s integrity is key. Since there is a wide variety of coolant formulations to meet proper regulations, recognizing and knowing the coolant formulation is critical.
Consider the below points:
a. Chemistry issues
• Mixing
• Maintaining proper fluid corrosion inhibitor levels
• Understanding equipment recommendation for glycol to water concentrations
b. Contamination issues
• Air leaks
• Internal/External contamination concerns
Transportation
Rising inflation, high fuel prices, and changes in supply availability demands have prioritized the need for keeping equipment in operation and extending all fluid life. Monitor the below common coolant system concerns as part of an effective predictive maintenance program:
a. High Temperature Issues
• Glycol concentration
• Freeze point and boil point protection
b. Chemistry issues
• Corrosion inhibitor
• Mixing
c. Contamination
• Scale hardness
• Glycol degradation
To conclude, each industry may have different demands for coolants, but their goals remain the same: to maintain equipment and get the very best out of the equipment for as long as possible. There is no shortcut to maintaining your coolant but proper fluid analysis and monitoring. The earlier the concerns, the better the chances to avert premature failure.