How to maintain mixed fleet to improve performance?
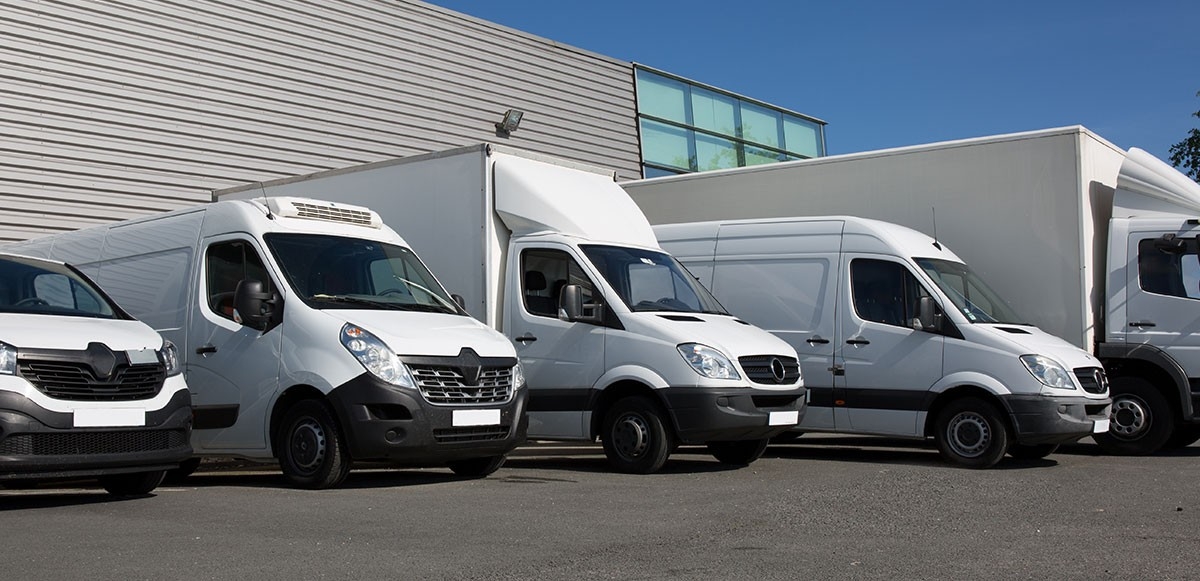
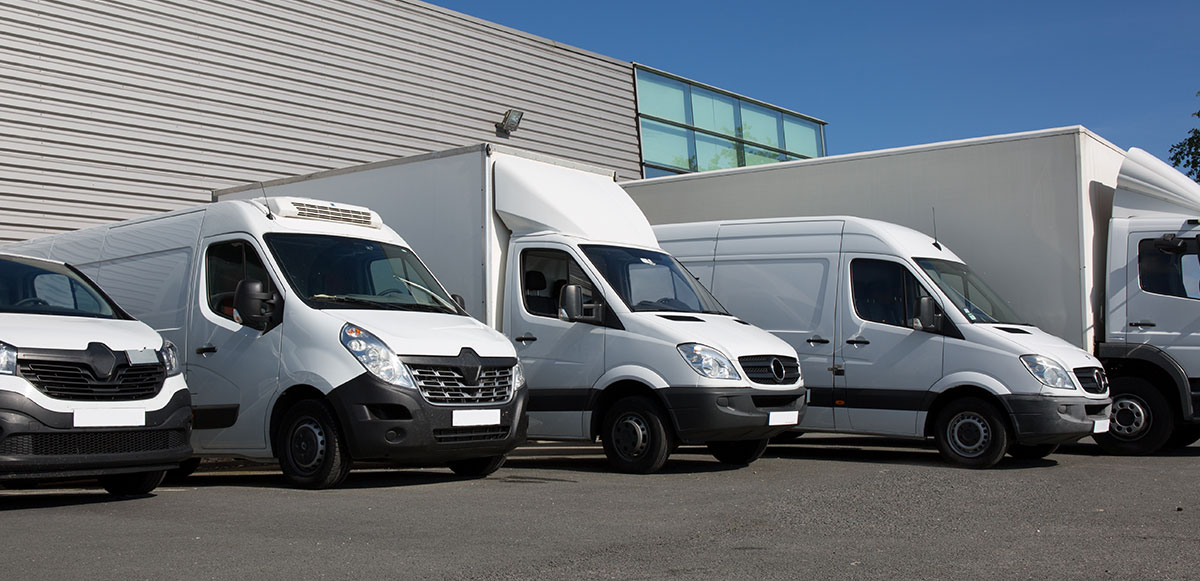
Maintaining a mixed fleet is no easy task. Many managers take a traditional approach to maintenance schedules and oil drain intervals by trying to find a common interval that works across the fleet. The reasoning behind this conservative schedule is that they believe this will eliminate the need for regular oil analysis.
However, what these managers don’t understand is that oil analysis is not only about oil. Through oil analysis you can recognize all kinds of problems with your equipment –fuel dilution, dirt contamination, coolant leakage, or some other issue that could undermine performance. Oil analysis helps you predict and possibly avoid unforeseen equipment failures.
By setting up one common maintenance schedule across one's fleet, and removing oil analysis, one may increase material and labor costs, while raising one's risk of failure on any machine by up to 11%.
For example, take a common piece of equipment, such as a scraper. Oil changes, including the cost of oil, filters, spent oil and labor, cost about $1,540 a year. Assuming one’s fleet has 100 similar machines getting oil service four times a year, then one ends up spending $154,000 annually on lubricant changes. By conducting regular oil analysis, one could, on average, eliminate at least one oil change per machine per year. Without regular oil analysis, one’s expenditure is an additional $38,500 annually than one needs. But this expenditure doesn’t include downtime, which can be significantly higher than the material cost savings.
Without regular oil analysis, one can also reduce the ability to predict common equipment failures. Did you know that 40% of engine failures are related to cooling system contamination, which an oil analysis can detect? In short, this conservative approach to the maintenance schedule can cost roughly $130,000 a year.
A comprehensive preventive maintenance program that allows one to keep track of all OEM required intervals, schedule maintenance while also including regular oil analysis, which can cut lubricant consumption by an average of 25% resulting in higher equipment availability and utilization.
To conclude, remember to service the right equipment at the right time, and be alerted to potential failures before they occur, as this will not only reduce one’s material costs but also optimize productivity and maximize the return on investment for each vehicle.